જટિલ યંત્રભાગો બનાવતી વખતે ઘણીવાર અગાઉના પ્રક્રિયાને કારણે ખરબચડા થયેલ બાહ્ય આકારને ફિનિશ કરવું, તે ખૂબ જ અઘરી પ્રક્રિયા હતી. આ સમસ્યા ખાસ કરીને ઑટોમોટિવ ઉદ્યોગમાં ઘણીવાર અનુભવાય છે. ટ્રૂમ્ફ કંપનીએ જટિલ કાર્યવસ્તુઓનું યંત્રણ સરળતાથી કરવા માટે ટ્રૂ લેઝર સેલ 5030 મશીન વિકસાવ્યું છે. આ મશીન વિશે ઉદાહરણસાથે માહિતી આપનારો લેખ.
લેઝર (લાઈટ ઍમ્પ્લિફિકેશન બાય સ્ટિમ્યુલેશન એમિશન ઑફ રેડિએશન) એટલે રેડિએશનના ઉત્તેજિત ઉત્સર્જન દ્વારા પ્રકાશ પરિવર્ધન. પ્રકાશ પટલમાં રહેલ ઇલેક્ટ્રોમૅગ્નેટિક લહેરોની શક્તિ, ઉત્સર્જનની પ્રક્રિયા દ્વારા વધારીને પ્રકાશ કિરણોનું એક બીમમાં રૂપાંતર કરવાની આ એક અદ્યતન પદ્ધતિ છે. સાંકડી તરંગલંબાઇ, ઇલેક્ટ્રોમૅગ્નેટિક સ્પેક્ટ્રમ અને લગભગ એક જ રંગના પ્રકાશ કિરણોના આ ઉત્સર્જીત શલાકાને લેઝર બીમ કહેવાય છે. આ શલાકા ઘણું કરીને એકરેખીય અને સાંકડી હોય છે અને તે અલગ અલગ લેન્સ અથવા ફાઈબર કેબલની મદદથી આપણી અપેક્ષિત જગ્યાએ પહોચાડી શકાય છે. એક ઉચ્ચ કક્ષાની ટેકનોલોજીનો વિકાસ કરીને લેઝરની મદદથી આજે આધુનિક જગતમાં અનેક કામો સરળ થઈ ગયા છે.
લેઝર મશીનના ઉત્પાદનમાં અગ્રેસર હોય તેવા 'ટ્રુમ્ફ' કંપનીએ ત્રિમિતીય (3D) યંત્રણ (મશીનિંગ) ક્ષેત્રમાં સર્વ આકારના ભાગ, વિવિધ આકારની ટ્યૂબ વગેરે જેવી જટિલ કાર્યવસ્તુનું અપેક્ષિત યંત્રણ સરળતાથી કરવા માટે 'ટ્રુ લેઝર સેલ 5030' આ મશીન વિકસિત કરેલ છે.
આ મશીન વાપરીને લેઝર કટિંગ પ્રક્રિયાથી સર્વ પ્રકારના ધાતુ અને અન્ય ઘટકોનું અત્યંત ચોકસાઈપૂર્વક યંત્રણ કરી શકાય છે. લેઝર બીમ યોગ્ય પદ્ધતિથી નિયંત્રિત કરવામાં આવે છે. પ્રચંડ ઉર્જા હોય એવી આ કિરણનું બીમ જ્યારે સૂક્ષ્મતમ સમયમાં ધાતુના સંપર્કમાં આવે છે, ત્યારે જે ભાગ સાથે સંપર્ક થયો હોય, માત્ર તે જ ભાગ પળવારમાં પીગળવા લાગે છે. જો ઉર્જાનું પ્રમાણ યોગ્ય હોય તો બીમ આરપાર જાય છે. આ રીતે જ ધાતુના યંત્રણનું કાર્ય શરુ થાય છે. કોઈપણ પદાર્થ કાપવા માટે અનેક પદ્ધતિઓ ઉપલબ્ધ હોવા છતાં લેઝર પ્રણાલી દ્વારા પદાર્થ સાથે પ્રત્યક્ષ સંપર્ક કર્યા વિના અન્ય આકાર ન બગડે અને છતાં યંત્રણનું ધાર્યું કામ ઓછામાં ઓછા સમયમાં પાર પડે છે.
આ પ્રક્રિયા ઓછા સમયમાં થાય છે અને અત્યંત સૂક્ષ્મ સપાટી પૂરતી મર્યાદિત હોય છે. તે કારણે નિર્માણ થનાર કાપાની પહોળાઈ અત્યંત સૂક્ષ્મ હોય છે અને તેની આસપાસના વિસ્તારમાં કોઈ વિપરીત અસર થતી નથી. આ ક્રિયામાં અપેક્ષિત આકાર ગમે તેટલો જટિલ હોય, તો પણ તેનું યંત્રણ સચોટતાથી થાય છે. આ પદ્ધતિમાં એની લવચીકતાને કારણે જ્યાં વિવિધ આકારના અને નાની સંખ્યામાં યંત્રભાગ અથવા નમૂના કાર્યવસ્તુ તૈયાર કરવાની હોય, ત્યાં એ માટે લેઝર ટેકનોલોજીનો ઉપયોગ સફળતાપૂર્વક કરી શકાય છે.
કાપવાના ભાગની ધારનું મહત્ત્વઅન્ય યંત્રણ પ્રક્રિયાઓમાં ગરમી નિર્માણ થવાને કારણે ઘણા દુષ્પરિણામો ઉદ્ભવતા હોય છે, તેમજ યંત્રભાગની ધાર ખરબચડી થાય છે. લેઝર કટિંગમાં અલ્ટ્રા શૉર્ટ પલ્સ અથળાઈને યંત્રણ થતુ હોવાથી, એવું કશું જ થતું નથી. વૈદ્યકીય ઉપકરણો, હૃદયની રક્તવાહિનીઓમાં વાપરવામાં આવતા સૂક્ષ્મ આકારના સ્ટેન્ટ વગેરે કાર્યવસ્તુ નિર્માણ કરવામાં લેઝરનો ઉપયોગ કરવામાં આવે છે.
લેઝર દ્વારા યંત્રણ પ્રક્રિયા કોઈપણ ધાતુના અપેક્ષિત યંત્રણની ક્રિયા કેવી રીતે થતી હોય છે તે આપણે ચિત્ર ક્ર. 4 પરથી સમજી લઈએ.
કાર્યવસ્તુની સપાટી પર યોગ્ય પ્રકારે કેન્દ્રિત કરેલ લેઝર કિરણ જે જગ્યાએ ટકરાય છે, ત્યાં અત્યંત ઉષ્ણતાને કારણે તેટલો નિયંત્રિત ભાગ બળી જાય છે અને કટિંગ થાય છે. આ પ્રક્રિયામાં અનેક ઘટકોનું યોગદાન હોય છે.
1. ફોકસિંગ ઑપ્ટિક્સ : વિશિષ્ટ લેન્સની મદદથી લેઝર બીમ અપેક્ષિત જગ્યાએ કેન્દ્રિત કરવામાં આવે છે.
2. તાપમાન : લેઝર બીમ કાર્યવસ્તુની સપાટી પર જ્યારે ટકરાય છે, ત્યારે તે ભાગનું તાપમાન એટલું વધી જાય છે કે એ ભાગ નિયંત્રિત રીતે પીગળવા લાગે છે.
3. કટિંગ ગૅસ : ઉપર વર્ણવેલ ક્રિયા થયા બાદ પીગળી ગયેલા કણ ગૅસની મદદથી બહાર કાઢવામાં આવે છે. એ ગૅસ ચિત્ર ક્ર. 4 માં દર્શાવ્યા પ્રમાણે લેઝર બીમ સાથે જ છોડવામાં આવે છે.
4. ડ્રૅગ લાઈન : કાર્યવસ્તુની સપાટી પર જ્યાં યંત્રણ કરવાનું હોય, ત્યાં એ બીમ એવી રીતે ફેરવવામાં આવે છે, કે યંત્રણ કરવામાં આવેલ ભાગો પર લેઝર બીમની મુવમેન્ટ સાથે સમાંતર ડ્રેગ લાઈન નિર્માણ થાય છે.
5. મેલ્ટ : કાર્યવસ્તુનો નિયંત્રિત પીગળેલો ભાગ.
6. કટિંગ પૉઈન્ટ (Kerf width) : કાર્યવસ્તુની સપાટી પર નિર્માણ થયેલ ખાંચાનો આકાર આ લેઝર બીમની પહોળાઈ કરતા તદ્દન નજીવી માત્રામાં વધુ હોય છે.
7. નૉઝલ : લેઝર બીમ અને કટિંગ ગૅસ એક સાથે નિયંત્રિત જગ્યા પર છોડવાનું કાર્ય નૉઝલ કરે છે.
8. યંત્રણની દિશા : નૉઝલ હેડ અથવા કાર્યવસ્તુની નિયંત્રિત મુવમેન્ટને લીધે યંત્રણની દિશામાં ખાંચો તૈયાર થાય છે.
લેઝર કટિંગ પ્રક્રિયા પર અપેક્ષિત પરિણામ કરનાર ઘટકો• કેન્દ્રીય લંબાઈ અને કેન્દ્રીય વ્યાસ (ફોકલ લેન્થ અને ફોકલ ડાયામીટર) : લેઝર કિરણોની કાર્યવસ્તુના વિશિષ્ટ ભાગોથી કેન્દ્રીય લંબાઈ અને કેન્દ્રીય વ્યાસ, એના આધારે યંત્રણની જગ્યા અને ખાંચાની પહોળાઈ નિશ્ચિત કરાય છે.
• લેઝર ઉર્જા : કાર્યવસ્તુનો અપેક્ષિત આકાર મળી શકે તે માટે વિશિષ્ટ અને ચોક્કસ માત્રાની ઉર્જા નિર્માણ થાય એ જરૂરી છે, એમાં લેઝર કિરણોની શક્તિ અને કિરણો દ્વારા આચ્છાદિત ભાગનો ગુણોત્તર મહત્ત્વનો છે.
• નૉઝલનો વ્યાસ : લેઝર બીમ અને કટિંગ ગૅસ, નૉઝલમાંથી એકત્ર બહાર નીકળે છે અને તેથી જ યોગ્ય ગુણવત્તા માટે નૉઝલનો આકાર યોગ્ય રાખવો જરૂરી છે.
• કામની પદ્ધતિ : લેઝરનો અવિરત પ્રવાહ અથવા નિશ્ચિત સમય માટે અથળાતા બીમનું આયોજન કામની પદ્ધતિ પ્રમાણે કરવામાં આવે છે.
• કટિંગ ગૅસ અને કટિંગ પ્રેશર : આર્ગૉન અથવા નાઈટ્રોજન જેવા ન્યૂટ્રલ કટિંગ ગૅસ વાપરવાને કારણે એમની કાર્યવસ્તુના પીગળેલા કણો સાથે રાસાયણિક પ્રક્રિયા થતી નથી. ગૅસનું નિયંત્રિત પ્રેશર, આ કટિંગ પ્રક્રિયા અપેક્ષિત પદ્ધતિથી થવા માટે સહાયરૂપ બને છે, તેમજ પીગળેલ કણોનો બાહ્ય વાતાવરણ સાથે સંપર્ક થવા દેતો નથી.
• યંત્રણ ગતિ : ધાતુની જાડાઈ જેમ જેમ વધતી જાય તેમ તેમ યંત્રણની ગતિ ઘટતી જાય છે. યંત્રણ ગતિનો ગુણોત્તર યોગ્ય ન રાખવામાં આવે, તો સપાટી ખરબચડી બને છે, બર રહી જાય છે અને સપાટીનું અપેક્ષિત ફિનિશ નથી મળતું.
ટ્રુ લેઝર સેલ 5030આપણે ઉપર જોયું કે જટિલ યંત્રભાગો તૈયાર કરતી વખતે ઘણી વખત તેની અગાઉની પ્રક્રિયાને કારણે ખરબચડી થઈ ગયેલ બાહ્ય સપાટી સાફ કરવી એ અત્યંત જટિલ પ્રક્રિયા હોય છે. ખાસ કરીને વાહન ઉદ્યોગમાં આવા ભાગો મોટા પ્રમાણમાં ઉપયોગમાં લેવાતા હોય છે. 3D લેઝર યંત્રણ કરવા માટે ટ્રુ લેઝર સેલ 5030 આ મશીન વાપરીને આ કામ સહજતાથી થઈ શકે છે. આમાં સૉલિડ સ્ટેટ લેઝરનો ઉપયોગ કરવામાં આવ્યો છે.
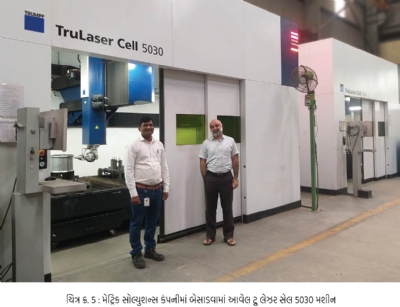
3D લેઝર યંત્રણ કરતી વખતે યંત્રભાગ ટેબલ પર સ્થિર રાખવામાં આવે છે. એ સિવાય જે કાર્ય કરવાનું હોય છે, એનો પ્રોગ્રામ મશીનમાં લોડ કરવામાં આવે છે. અપેક્ષિત જગ્યા પરનું મટીરિયલ કાઢવાનું કાર્ય કરતી વખતે નૉઝલ X, Y, અને Z એ ઉપરાંત C અક્ષ પર 360° અને B અક્ષ પર ±135° માં ટૉર્ચ સાથે ફરે છે. એ કારણે અલગ અલગ આકારની ટ્યૂબ્સ, સીટના અનેક ભાગો વગેરે પ્રકારના અનેક યંત્રભાગોનું યંત્રણ સહજતાથી કરાય છે. આ નવીન શ્રેણીમાં ‘ X બ્લાસ્ટ’ તકનીક શામેલ છે. એમાં યંત્રભાગ અને નૉઝલ, બન્ને વચ્ચેનું અંતર વધુ રાખવાથી નૉઝલ અથળાઈ જવું, વગેરે અકસ્માત ટાળી શકાય છે અને ગુણવત્તા સુધરે છે. 3000 (X) x 1500 (Y) x 700 (Z) મિમી. રેંજ અને 2000-4000 W શક્તિના આ મશીન, ભારતમાં ઉપલબ્ધ છે.
સાધારણ પદ્ધતિથી અનેક મશીન વાપરીને યંત્રણ કરવાને બદલે, એકલું ટ્રુ લેઝર સેલ 5030 મશીન વાપરવાથી કુલ ખર્ચમાં અંદાજે 20% જેટલી બચત થઈ શકે છે. એક જ મશીન સર્વ પ્રકારના કામો માટે ઉપયોગી સાબિત થવાથી મશીન શૉપની જગ્યામાં પણ બચત થાય છે. અગાઉ કોઈ એક નવીન યંત્રભાગનું (ઉદાહરણ તરીકે ઍક્ઝોસ્ટ પાઈપ) ટ્રિમિંગ કરવાનું હોય, તો તેના સેટિંગમાં જ 4 થી 5 કલાક લાગતા હતા. હવે જો ગ્રાહક પાસેથી નવો યંત્રભાગ અને તેના પ્રોગ્રામની ફાઈલ આવે, તો તરત જ એક કલાકમાં તે પ્રોગ્રામનો ઉપયોગ કરીને તત્કાળ ટ્રિમિંગ કરી શકાય છે. અનેક નવા યંત્રભાગોનો વિકાસ ઝડપથી કરવો આ કારણે શક્ય બનેલ છે.
ટ્રુ લેઝર સેલ પર અલગ અલગ આકારના અને 12 મિમી. જાડાઈના સ્ટીલના ભાગો પર, તેમજ 120 મિમી. સુધીના વ્યાસના અલગ અલગ ટ્યૂબ જેવા ગોળાકાર ભાગો પર યોગ્ય આકારનું યંત્રણ સરળતાથી કરી શકાય છે. એ માટે વિવિધ આકારના ફિક્શ્ચર માંગ મુજબ મળી શકે છે.
ઉદાહરણપુણેની બાજૂમાં ભોસરી ખાતે ‘મેટ્રિક્સ સોલ્યુશન્સ’ આ કંપનીમાં અમારું ટ્રુ લેઝર સેલ 5030, મશીન કાર્યરત છે. ત્યાંના વ્યવસ્થાપકીય ડાયરેક્ટર સંજય પનવાર અને લેઝર વિભાગના પ્રમુખ પ્રકાશ ગારળે આ મશીન વિશે પોતાનો અભિપ્રાય વ્યક્ત કરતા કહ્યું, “પાછલા ઘણાં વર્ષોથી વાહન ઉદ્યોગમાં વિવિધ વિભાગોમાં પર્યાવરણ સંબંધી સંશોધન અને વિકાસ ઝડપથી થઈ રહ્યો છે. વાહનોના ભાગોનું વજન ઓછું કરવું અને પર્યાવરણપૂરક વાહનોનું નિર્માણ કરવું, એ ઉદ્યોગની પ્રગતિ માટે અત્યાવશ્યક બનેલ છે. ખાસ કરીને BS-VI ધોરણ અમલમાં આવ્યા બાદ વાહનના બાહ્ય ભાગો અને ઍક્ઝોસ્ટ સિસ્ટમના અનેક નવા યંત્રભાગ નિર્માણ કરવામાં આવેલા છે. વિવિધ પ્રકારના ધાતુ, કાચ, પ્લાસ્ટિક અને અન્ય અનેક યંત્રભાગ વિકસિત કરવામાં આવી રહ્યા છે અને એમાં વિકાસ પ્રક્રિયા દરમિયાન સતત બદલાવ થતો રહેતો હોય છે. ઓછી જાડાઈના પરંતુ તેટલી જ તાકાદ હોય, તેવી વસ્તુઓનું નિર્માણ કરવામાં આવે છે. એમાંથી કેટલાક ભાગ બ્રિટલ હોવાથી જો ખોટી પદ્ધતિનો ઉપયોગ કરીને યંત્રણ કરવામાં આવે, તો તે તરત જ તૂટી શકે છે.’
“પ્રત્યેક ભાગની પ્રક્રિયામાં બાહ્ય ઢાંચો (બ્લૅન્ક) તૈયાર કરવા, ધારોનું કાળજીપૂર્વક કટિંગ કરવું, 3D આકારમાં ધારનું કાળજીપૂર્વક કટિંગ કરવું વગેરે બાબતો માટે વિવિધ આકારની ડાય અને ફિક્શ્ચર બનાવવા પડે છે. એ કારણે આવા પ્રકારના વિકાસની પ્રક્રિયા અત્યંત ખર્ચાળ હોય છે.”
“ટ્રુ લેઝર સેલ 5030 મશીન વાપરવાની શરૂઆત કર્યા બાદ મેટ્રિક્સ સોલ્યુશન્સમાં આ કાર્યને ગતિ મળી. નમુના યંત્રભાગ (પ્રોટોટાઈપ) નમૂના મુજબ ઝડપી તૈયાર કરી આપનાર કંપની ઝડપી પ્રગતિ કરી શકે છે, એ અહીં સ્પષ્ટ રૂપે દર્શાય છે. વિવિધ નમૂના યંત્રભાગમાં નહિવત ફેરફાર હોઈ શકે છે, પણ એ માટે દર વખતે અલગ અલગ ડાય બનાવવી શક્ય નથી. તેમ જ શરુઆતના ઉત્પાદનમાં વિવિધ તપાસ માટે 50 થી 100 જેટલા જ ભાગ બનાવવામાં આવે છે. ડાય તૈયાર કરીને તે બનાવવા, એ ખર્ચાળ સાબિત થાય છે. ટ્રુ લેઝર સેલ 5030 મશીન પર આવા ભાગ સરળતાથી બનાવી શકાય છે. આ મશીન પર 5 અક્ષીય કટિંગ કરવું શક્ય છે. પ્રેસ પાર્ટ, ડાય પાર્ટ, એવા કોઈપણ પ્રકારના ભાગ અમે બનાવી શકીએ છીએ. 10 મિમી. જાડાઈનું સ્ટેનલેસ સ્ટીલ, 3 મિમી. જાડાઈના ઍલ્યુમિનિયમ ભાગ, તેમજ કોઈપણ આકારના શીલ્ડ વગેરે ભાગ અમે ગ્રાહકની માગણી અનુસાર અને બને તેટલી ઝડપથી તૈયાર કરી શકીએ છીએ.”
“અમારે ત્યાં અમે લેઝર યંત્રણ માટે બે મશીન બેસાડેલા છે. શરૂઆતનો ખર્ચ વધુ હતો, પરંતુ પોતાનો ટૂલ રૂમ અને ઉપરાંત બે ટ્રુ લેઝર સેલ 5030 મશીન હોવાને કારણે, ઓર્ડર જલ્દી પૂર્ણ કરવાની અમારી ક્ષમતા વધી ગઈ છે. નવા યંત્રભાગ માટે માત્ર ડાય બનાવવા માટે અમને પહેલા લગભગ પાંચ દિવસ લાગતા હતા. હવે એ કામ પ્રોગ્રામ ફાઈલ લોડ કરીને માત્ર એક જ કલાકમાં થઈ જાય છે. એ કારણે અમારો પ્રતિસાદનો સમય (રિસ્પૉન્સ ટાઈમ) પણ સુધરી ગયો, કામની ગુણવત્તા પણ સુધારી. અત્યંત ઉત્તમ ફિનિશનું ટ્રિમિંગ અને તે પણ ઓછામાં ઓછા સમયમાં અમે કરી શકીએ છીએ. આ મશીન માટે માત્ર ગૅસ અને વીજળીની જરૂર પડે છે. અન્ય કોઈપણ ટૂલનો ખર્ચ થતો નથી. કુલ ખર્ચમાં અમે 40% બચત કરી શક્યા. આ બધાના એકત્રિત પરિણામ તરીકે ગ્રાહકોને અમારી તરફ વાળવામાં અમે સફળ થયા.”
“વિવિધ વાહનોમાં વપરાતા B પિલર, X મેમ્બર જેવા નવા નમુના યંત્રભાગ તૈયાર કરવા એ અમારી ખાસિયત છે. અમારી પાસે ટ્રુ લેઝર સેલ 5030 મશીન હોવાથી ઓછામાં ઓછા ટૂલિંગનો ઉપયોગ કરીને અમે એને બનાવી શકીએ છીએ. અમે ખાસ કરીને બ્લૅન્કિંગ અને ટ્રિમિંગ જેવા જટિલ કાર્ય માટે લેઝર મશીન વાપરીએ છીએ. આ મશીન ઓછી જગ્યા રોકે છે. હવે કોઇપણ જટિલ આકારના ભાગો નિર્માણ કરવાની અમારી તૈયારી છે.”
“નવું મશીન બેસાડતી વખતે ટ્રુમ્ફ કંપનીએ અમારા સ્ટાફને સર્વ પ્રકારનું પ્રશિક્ષણ (ટ્રેનિંગ) આપવાની વ્યવસ્થા કરી હતી. તે સિવાય હું એ પણ ખાતરીપૂર્વક કહી શકું છું, કે ટ્રુમ્ફ કંપનીએ વેચાણ પછીની સેવામાં સર્વ પ્રકારનો સપોર્ટ ઉત્તમ રીતે આપેલ છે.”