ઘણીવાર યંત્રભાગના તકનીકી ચિત્રમાં (મશીન ડ્રૉઇંગ) છિદ્ર તથા બાહ્ય વ્યાસના વર્ણનમાં ડિઝાઈનર ગોળાઈ (રાઉન્ડનેસ) અને નળાકારિતા (સિલિન્ડ્રિસિટી) પર મર્યાદા મૂકે છે. આ બન્ને સંજ્ઞાઓ અલગ અલગ ભૌમિતિક ગુણધર્મો દર્શાવે છે. પણ એ બંનેના નિયંત્રણ માટે કરવામાં આવતી પ્રક્રિયા સમાન હોવાથી આપણે એમના વિશે એક સાથે જ વિચાર કરીએ. સૌ પ્રથમ આપણે એ બંનેની વ્યાખ્યા અને અર્થ સમજીએ.
ગોળાઈ અથવા ગોળપણું
આ બંને સમાન અર્થના શબ્દ એક જ લાક્ષણિકતા દર્શાવવા માટે ઉપયોગમાં (ચિત્ર ક્ર. 1) લેવામાં આવે છે. બે કાલ્પનિક સમકેન્દ્રિય વર્તુળોની ત્રિજ્યાનો તફાવત એટલે ગોળાઈ. એમાં એ કાર્યવસ્તુની પરિમિતિ પરના તમામ બિંદુનો સમાવેશ હોય છે. એનાથી એ બાબત સ્પષ્ટ થાય છે કે એ લાક્ષણિકતા નળાની અથવા છિદ્રની પૂર્ણ સપાટી સાથે નહિ, પણ માત્ર એક જ ભાગ સાથે સંબંધિત હોય છે.
ચિત્ર ક્ર. 1 : ગોળાકાર કાર્યવસ્તુ
નળાકારિતા
એક નળાકારના બધા બિંદુ, જે બે સમકેન્દ્રિય નળાકારની વચ્ચે હોય છે, એ બે નળાકારોની ત્રિજ્યાના તફાવતને નળાકારિતા (ચિત્ર ક્ર. 2) કહેવાય છે. એનાથી એ બાબત સ્પષ્ટ થાય છે કે આ લાક્ષણિકતા નળાકારની પૂર્ણ સપાટી સાથે સંબંધિત છે, કોઈ એક ભાગ સુધી સીમિત નથી.
જરૂરત અનુસાર અથવા કોઈપણ વિશેષ કારણો માટે ઉપયોગમાં લેવાતા ‘ફિટ’ મુજબ, ડિઝાઈનર દ્વારા ગોળાઈ અથવા નળાકારિતા પર મર્યાદા નિશ્ચિત કરવામાં આવે છે.
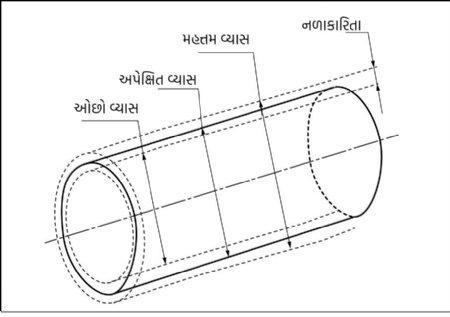
ચિત્ર ક્ર. 2 : નળાકાર કાર્યવસ્તુ
બોઅરિંગમાં સમસ્યા
હવે આપણે એ સમજી લઈએ કે ‘બોઅરિંગ’ પ્રક્રિયામાં ગોળાઈ અને નળાકારિતા પર કેવી રીતે અસર થાય છે અને એના પર કેવી રીતે નિયંત્રણ કરવામાં આવે છે.
કાર્યવસ્તુ પકડનાર ઘટકોનો પ્રભાવ
કાર્યવસ્તુ પકડવાના બળથી કાર્યવસ્તુ બેડોળ (ડિસ્ટૉર્ટ) ન થઈ જાય, તે માટે તેના પર નિયંત્રણ રાખવું જરૂરી છે. જ્યારે ટૂલ ફેરવીને બોઅરિંગ કરવામાં આવે છે, ત્યારે કાર્યવસ્તુના આકારમાં થતો બદલાવ, કાર્યવસ્તુને ફિક્શ્ચરમાં કેવી રીતે પકડી છે, તેના પર નિર્ભર કરે છે. જ્યારે કાર્યવસ્તુ ફેરવીને બોઅરિંગ કરવામાં આવે છે, ત્યારે કાર્યવસ્તુના આકારમાં થતો બદલાવ, જૉ અને કાર્યવસ્તુની વચ્ચેના સપાટીય સંપર્ક (ઇન્ટરફેસ) પર નિર્ભર કરે છે. ગોળ ફરતા ટૂલથી યંત્રણ કરતી વખતે એક સરળ પરીક્ષણ કરી શકાય છે. કાર્યવસ્તુ ફિક્શ્ચરમાં બેસાડ્યા બાદ જે ભાગ પર બોઅરિંગ કરવાનું હોય તે ભાગ પર એક ડાયલ ઇન્ડિકેટર રાખવામાં આવે છે. રેસ્ટ પૅડ પર સેન્સર માત્ર અડે એટલું જ પકડનું દબાણ રાખી, ડાયલ શૂન્ય પર લાવીને પકડનું દબાણ જરૂરત મુજબ વધારવામાં આવે છે. જો આ દરમિયાન ડાયલની સોય હલી જાય, તો એવું માનવામાં આવે છે કે કાર્યવસ્તુમાં બેડોળપણું આવી રહ્યું છે. ડાયલ 90° માં ફેરવવાથી, બેડોળપણાની દિશા જાણી શકાય છે. આ પરીક્ષણ એ જ ભાગ પર કરવાથી એના ગોળાઈ પર પડતા પ્રભાવને જાણી શકાય છે.
નળાકારિતા પર જો સચોટ નિયંત્રણ મેળવવું હોય અને જો છિદ્રના આકાર અનુસાર બે ડાયલ ગેજ બેસાડવા સંભવ હોય, તો છિદ્રની શરૂઆતમાં એક અને અંતમાં એક, એમ બે ગેજ બેસાડવાથી લંબાઈની દિશામાં થનાર બેડોળપણા વિશે જાણકારી મેળવી શકાશે.
આ પરીક્ષણથી, ઑપરેટરને બેડોળપણાના સ્વરૂપનું અનુમાન આવી જતું હોય છે. યંત્રણની ટ્રાયલ લેતા પહેલા જરૂરી પ્રક્રિયાઓ કરી આ બેડોળપણા પર નિયંત્રણ મેળવી શકાય છે. ફિક્શ્ચર મશીન પર બેસાડતા પહેલા જ આ પરીક્ષણ કરવાથી, મશીનનો આ કારણે વેડફાતો સમય બચી જાય છે.
હવે એ જાણીએ કે લેથ મશીન પર (પરંપરાગત અથવા તો સી.એન.સી. મશીન) બોઅરિંગ કરતી વખતે શું થતું હોય છે. સામાન્ય રીતે લેથ પર 3 જૉ ચક (ચિત્ર ક્ર. 3) વપરાય છે. જૉના ઉપયોગથી કલૅમ્પિંગ કરતી વખતે ઘર્ષણાત્મક બળ દ્વારા પકડવાનું બળ મળે છે, જે યંત્રણ બળની વિપરીત દિશામાં કામ કરે છે. પણ જૉએ, પોતાના સંચલનની દિશામાં લગાડેલ બળને કારણે કાર્યવસ્તુનો આકાર બગડી શકે છે. અહીં સ્થિર ઘર્ષણનું સરળ સૂત્ર લાગુ પડે છે.
ચિત્ર ક્ર. 3 : જૉમાં પકડેલી કાર્યવસ્તુ
કાર્યવસ્તુની જાડાઈ ઓછી હોય તો બેડોળપણું ટાળવું વધુ પડકારરૂપ હોય છે. આવા સમયે ઘર્ષણનું બળ વધારી જૉ દ્વારા લગાડવામાં આવેલ બળ ઓછું રાખવું પડે છે. જૉનું બળ ઓછું કરવા માટેનો એક વિકલ્પ છે, દબાવ એટલો જ રાખી સંપર્ક ક્ષેત્ર વધારવું. ઘણીવાર વિશેષ જૉ (ચિત્ર ક્ર. 4) તૈયાર કરવા પડતા હોય છે, જેથી એ સંપર્ક ક્ષેત્રો પ્રતિ જૉ 100° થી 110° મળે. આવા જૉનું કાર્યવસ્તુને અનુરૂપ, અચૂક બોઅરિંગ કરવું પડતું હોય છે. એનાથી કાર્યવસ્તુ બેડોળ થવાની શક્યતા ઓછી હોય છે.
ચિત્ર ક્ર. 4 : જૉ
ઘર્ષણનો સહગુણાંક વધારવા માટે જૉની સપાટી ખરબચડી કરવી પડે છે. એના પર સરેશન કરવા પડે છે અથવા તો એને ખોતરવું પડે છે. પણ જો સરેશન કરવામાં આવે તો એના ચિહ્ન, જૉ દ્વારા જકડવામાં આવેલ સપાટી પર દેખાય છે. એટલે જ્યારે પકડવામાં આવનાર સપાટીનું યંત્રણ કરવામાં ન આવ્યું હોય ત્યારે અથવા તો આ ચિહ્નો હોવા છતા કોઈ ફર્ક ન પડતો હોય, તો જ સરેશન કરેલ જૉનો ઉપયોગ કરવામાં આવે છે. ચકને કારણે આકારમાં થતું બેડોળપણું આવા ઉપાયો અજમાવી ઘટાડી શકાય છે.
સ્પિન્ડલના ડાયનૅમિક્સની અસર
કેમકે આ સ્પિન્ડલ ગોળ ફરતો ભાગ હોય છે, કાર્યવસ્તુની ગોળાઈ પર એની અસર થાય છે. કર્તન દબાણને કારણે સારું સ્પિન્ડલ ક્યારે પણ ધક્કા અથવા આંચકા નથી આપતું, પણ બોઅરિંગમાં ક્લિઅરન્સ વધવાને કારણે સ્પિન્ડલ ધક્કા મારી શકે છે. યંત્રણ કરતી વખતે સ્પિન્ડલ જો હલી જાય તો કાર્યવસ્તુ અપેક્ષિત ગોળાઈની ન બની અંડાકાર (ઓવલ) અથવા તો અન્ય આકારની બને છે. એવા આકારના છિદ્રો વધુ અંડાકાર (એલિપ્ટિકલ) પણ કહેવાય છે. ઘણીવાર ખાલી સ્પિન્ડલ ફેરવ્યા પછી ‘રન આઉટ’ નથી એમ દેખાય છે, પણ એના પર ભાર (લોડ) વધવાથી એની ખામી જણાય છે. એટલા માટે મશીન ઉત્પાદક દ્વારા સૂચવવામાં આવેલ પ્રતિબંધાત્મક તથા અનુમાનિત (પ્રિવેન્ટિવ અને પ્રેડિક્ટિવ) તંત્રના ઉપયોગથી સ્પિન્ડલનો સમયસર મેન્ટેનન્સ કરવો જરૂરી હોય છે.
કાર્યવસ્તુ અથવા ટૂલની રચના અથવા વજનના ઘાટને કારણે, એને સ્પિન્ડલ પર બેસાડવાથી સ્પિન્ડલનું સંતુલન બગડી જાય છે. ખાસ કરીને સ્પિન્ડલની ગતિ (આર.પી.એમ.) વધવાથી ગતિશીલતામાં અસંતુલન વધે છે, જેથી સ્પિન્ડલ આંચકા ખાય છે. એનાથી ગોળાઈ તો બગડે જ છે, સાથે સાથે ટૂલની આવરદા પણ ઘટે છે. એનો ઉપાય છે, બોઅરિંગ ટૂલનું ગતિશીલ સંતુલન (ડાયનૅમિક બૅલન્સિંગ) કરવું અથવા કાર્યવસ્તુ ચકમાં બેસાડ્યા બાદ લેથના સંદર્ભે સંતુલન કરવું. ફરનારા પૂર્ણ ભાગનું ગતિશીલ સંતુલન કરવાથી ગોળાઈમાં સુધારો થાય છે.
યંત્રણ બળની અસર
યંત્રણ બળના અક્ષીય ભાગની અસર, બેડોળપણા પર અને અંતે ગોળાઈ પર પડે છે. આની અસર ઓછામાં ઓછી પડે તથા ચોકસાઈવાળું છિદ્ર બનાવવા માટે પૉઝિટિવ રેકવાળા ટૂલનો ઉપયોગ કરો. એ કારણે પ્રતિ કાર્યવસ્તુ ટૂલનો ખર્ચો ક્યારેક વધે છે, પણ કાર્યવસ્તુમાં ન્યૂનતમ ખામી હોવાને કારણે અસ્વીકૃતી થવાનું નુકસાન ઘટે છે. પ્રક્રિયા વારંવાર રીસેટ નથી કરવી પડતી, એનાથી સમય પણ બચે છે. આ મુદ્દાઓ પર વિચાર કરીને ઉચિત નિર્ણય લેવો પડે છે.
રેડિયલ યંત્રણ દરમિયાન તૈયાર થનારા બળ પર, ફિનિશિંગ કરતી વખતે હટાવવામાં આવેલ મટિરિયલ અને ટૂલના નોઝ ત્રિજ્યાની પણ અસર થાય છે. પણ સપાટીના ખરબચડાપણા પર નિયંત્રણ માટે એનો વધુ વિચાર કરવો પડે છે.
ઉષ્મીય બેડોળપણાથી થનાર અસર
સૂકા યંત્રણમાં ઉત્પન્ન થનાર ગરમીથી કાર્યવસ્તુનું તાપમાન વધે છે. યંત્રણ કર્યા પછી કાર્યવસ્તુ ફિક્શ્ચરમાંથી કાઢીને ખુલ્લામાં ઠંડી થવા માટે રાખવામાં આવે ત્યારે, છિદ્રની સપાટી પરથી નીકળનારી ગરમી છિદ્રની આસપાસના વજનના વિતરણ અનુસાર હોય છે. કાર્યવસ્તુની રચના અનુસાર, ગરમી અલગ અલગ ભાગમાંથી ભિન્ન માત્રામાં બહાર ફેંકવામાં આવે છે. એનાથી કાર્યવસ્તુ વિકૃત થઈ શકે છે, જેની અસર ગોળાઈ તથા નળાકારિતા પર થાય છે. આમ ઉષ્મીય બેડોળપણાથી બચવા માટે જ્યારે શક્ય હોય ત્યારે યંત્રણમાં શીતકનો ઉપયોગ કરો.
છિદ્રની લંબાઈથી થનારી અસર
જો છિદ્રની લંબાઈ વ્યાસની તુલનામાં વધુ હોય તો (L/D>5), તો ગોળાઈને બદલે નળાકારિતા પર અસર થવાની શકયતા વધુ હોય છે. જ્યારે વધુ લંબાઈના બોઅરિંગ બારનો ઉપયોગ કરવામાં આવે છે, ત્યારે કાર્યવસ્તુની રચના અથવા અન્ય સમસ્યાને કારણે લંબાઈ/વ્યાસનો ગુણોત્તર યોગ્ય રાખવો સંભવ નથી હોતો ત્યારે લંબગોળાકારિતા પર નિયંત્રણ ઘટી શકે છે. બોઅરિંગ બાર પર્યાપ્ત માત્રામાં કડક (સ્ટિફ) ન હોય, ત્યારે એના પર કર્તન બળની અસરને કારણે થનાર વિચલનનું (ચિત્ર ક્ર. 5) સચોટ અનુમાન લગાડવું મુશ્કેલ હોય છે. બોઅરિંગ બાર કડક બનાવવામાં માટે, એની ડિઝાઈન તથા ઉત્પાદનમાં અલગ અલગ તકનિકીનો ઉપયોગ કરાતો હોય છે. બોઅરિંગ બાર વધુ કડક બનાવવા માટે ઉત્પાદકો પાસે ઘણા પ્રકારના ઉપાય હોય છે. કુલ કિંમતનો વિચાર કરીને ઉચિત ઉપાય પસંદ કરવામાં આવે છે.
ચિત્ર ક્ર. 5
અલગ અલગ પ્રકારના યંત્રણ સમયે, ઉપર વર્ણવેલ તમામ ઘટકોની અસર, ઓછી અથવા વધુ પ્રમાણમાં ગોળાઈ અથવા નળાકારિતા પર થતી જ હોય છે. તમામ ઘટકોનું ઉચિત મૂલ્યાંકન કરીને એના પર નિયંત્રણ મેળવવા માટે દરેક યંત્રણના કિસ્સામાં યોગ્ય ઉપાયો કરવા પડતા હોય છે. ઘણીવાર ઉપરોક્ત ઘટકોની અસર થતી પણ નથી, પણ વર્તુળાકાર અથવા નળાકાર કાર્યવસ્તુનું ઉત્પાદન કરતી વખતે, એને ધ્યાનમાં રાખવા જરૂરી હોય છે.
9359104060
[email protected]
રાજેશ મ્હારોળકર મેકૅનિક્લ એન્જિનીયર છે અને તેમને ઔદ્યોગિક ક્ષેત્રનો 30 થી વધુ વર્ષોનો અનુભવ છે. હાલમાં તેઓ ઘણી બધી કંપનીઓમાં સલાહકાર તરીકે સેવા આપી રહ્યા છે.