વાહન, સામાન્ય એન્જિનિયરિંગ, મશીન ટૂલ, વિમાન અને પંપ ઉદ્યોગમાં આવશ્યક ઘણા પાર્ટના આકાર અને પરિમાણોં અનિયમિત હોય છે. સિલિન્ડર હેડ, કૅમશાફ્ટ, ક્રઁકશાફ્ટ, સિલિન્ડર બ્લૉક, કનેક્ટિંગ રૉડ, ગિયરબૉક્સ, રોટર બ્લેડ અને બીજા ઘણા ખાસ આકારના પાર્ટ અલગ અલગ જગ્યાએ વપરાય છે. એના અનિયમિત આકારને લીધે આવા પાર્ટનું ઉત્પાદન ફોર્જિંગ અથવા કાસ્ટિંગની પ્રક્રિયા દ્વારા કરાવામાં આવે છે.
આ પ્રક્રિયાઓમાં ડાય, પંચ અને મોલ્ડ વપરાય છે. ડાયમાં રહેલ આકાર માટે ખાસ NC પ્રોગ્રામ તથા કટિંગ ટૂલ જરૂરી હોય છે. આવા NC પ્રોગ્રામ UG-NX, CATIA, MASTERCAM જેવા 3D સોફ્ટવેરની મદદથી બનાવામાં આવે છે. પ્રોગ્રામ બનતી વખતે દરેક અલગ પ્રોફાઈલ માટે અલગ ટૂલ પસંદ કરવામાં આવે છે.
ડાય તથા મોલ્ડ માટે P20, ડાય સ્ટીલ જેવા ધાતુઓ વપરાય છે. ક્યારેક ક્યારેક ડાય અને મોલ્ડ માટે કાસ્ટ આયર્ન/એસ.જી. લોખંડ વપરાય છે. ડાયનું યંત્રણ કરવું મુશ્કેલ અને પડકારજનક છે. સોલિડ બ્લૉકથી, યંત્રણ દ્વારા બિનજરૂરી મટિરિયલ કાઢીને ઇચ્છિત અંતિમ આકાર મેળવવા માટે ઉત્પાદકનો ઘણો સમય વેડફાઇ જાય છે. ડાયમાં રહેલી જગ્યા, આકાર અને બાહ્ય બાજુને યંત્રણ કરવા માટે ખાસ આકારના ટૂલનો ઉપયોગ કરવો પડે છે. આ ભાગનું ત્રણ ડાયમેન્શનમાં યંત્રણ કરતી વખતે, ખાસ આકારને લીધે ટૂલની કટિંગ એજ, હંમેશા મટિરિયલના સંપર્કમાં હોવી જરૂરી છે. એટલા માટે આ કામ માટે વપરાતું ઇન્સર્ટ ગોળાકાર હોય છે અથવા ઇન્સર્ટના એજની ત્રિજ્યા વધારે હોય છે. આનાથી ટૂલનો બીજો કોઈપણ ભાગ યંત્રણ થનાર કાર્યવસ્તુને અડતો નથી અને અપેક્ષિત આકાર અથવા પ્રોફાઈલ પ્રાપ્ત કરી શકાય છે.
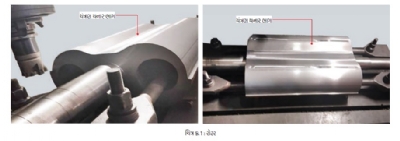
ન્યૂમૅટિક ભાગ અને ડાયના ઉત્પાદકની સાથે મળીને અમે એક પ્રયોગ કર્યો અને સુધારો પણ લાવ્યા. આ ઉત્પાદક અલગ આકારના હાઉસિંગ અને રોટર જેવા ન્યુમૅટિક પાર્ટ કાસ્ટિંગ પધ્ધતિથી બનાવે છે. આ પાર્ટ કાસ્ટિંગથી બનાવવામાં આવે છે એટલા માટે એની સપાટી ખરબચડી હોય છે અને સાચા ટૂલનું ચયન કરીને એને સુંવાળું અને ઉત્તમ ફિનિશ આપવું પડે છે. આ ઉત્પાદક અલગ આકારના રોટર બનાવે છે. આ રોટરમાં (ચિત્ર ક્ર. 1) બે અથવા ત્રણ કોટર (લોબ) હોય છે.
લોબની પહોળાઈ 154 મિમી. થી 1000 મિમી. સુધી અને લંબાઈ 80 મિમી. થી 1000 મિમી. સુધી હોય છે. યંત્રણ પ્રક્રિયા ત્રણ તબક્કામાં કરવામાં આવે છે.
• પ્રથમ (રફ) યંત્રણ : ત્રિકોણાકાર ઇન્સર્ટની મદદથી.
• મધ્યમ (સેમીફિનિશ) યંત્રણ : ગોળાકાર ઇન્સર્ટની મદદથી.
• અંતિમ (ફિનિશ) યંત્રણ : અર્ધગોળાકાર ઇન્સર્ટની મદદથી.
અમે પ્રથમ યંત્રણ માટે કરેલા સુધારાનું વર્ણન આ પ્રકારે છે.
કાર્યવસ્તુનું નામ : રોટરી (બે કોટરોવાળા)
પહોળાય : 60 મિમી.
લંબાઈ : 425 મિમી.
મટિરિયલ : કાસ્ટ આયર્ન
(હાર્ડનેસ 220-280 BHN)
યંત્રણ પ્રક્રિયા : રફ પ્રોફાઈલ મિલિંગ
મશીન : BMW 45-BT 40 વર્ટિકલ મશીનિંગ સેન્ટર
સમસ્યાઓ
અ. ઓછા ખૂણા ધરાવતી કટિંગ ધાર.
આ. ફીડ રેટ વધુ હોવાને કારણે ઇન્સર્ટની ચિપ નિકળવી.
ઇ. ટૂલની ઘટેલી આવરદા
નવી પદ્ધતિમાં અમે 4 ખુણાના નાના ઇન્સર્ટ વાપર્યા જેમાં વધારે મજબૂત ધાર અને ખુણાની ત્રિજ્યા 2 મિમી. હતી. વધુ મજબૂત પકડ઼ મેળવવા માટે ઍંગ્યુલર સ્ક્રૂથી ક્લૅમ્પિંગ કરવામાં આવ્યું.
SDMT 10 ની વિશેષતાઓ અને ફાયદા
1. વધુ ફીડ રેટ મેળવવા માટે કટિંગની મજબૂત ધાર.
2. ખૂણાઓની મોટી ત્રિજ્યા.
3. ઍંગ્યુલર સ્ક્રૂ કલૅમ્પિંગ માટે સ્ક્રૂના છિદ્રો મોટા હોવાથી પકડ વધુ મજબૂત બને છે.
4. ઍપ્રોચ ઍન્ગલ ઓછો હોવાને કારણે 1 મિમી. પ્રતિ દાંત જેટલા ફીડ રેટનો ઉપયોગ કરી શકાય છે.
5. કાપાની મહત્તમ ઊંડાઈ 1.2 મિમી. રાખી શકાય છે.
ફાયદા
1. ટૂલ ટૂટી જવાની સમસ્યા ન રહી.
2. ટૂલની આવરદા 33% થી વધી.
3. વધારે સખ્ત શ્રેણીના તથા ઘસારા પ્રતિકારની વધુ ક્ષમતાવાળા ઇન્સર્ટ વાપરવાથી વધુ ગતિ પર યંત્રણ કરવું શક્ય છે. આ શ્રેણી લોખંડ સિવાય બીજા ધાતુ, કાસ્ટ આયર્ન અને વધારે સખ્ત મટિરિયલ માટે ઉપયોગી છે.
4. એક કટરમાં વધુ ઇન્સર્ટ બેસાડી શકવાથી ફીડ રેટ થોડો વધારી શકાય છે.