પ્રસ્તુત લેખમાં આપણે ડ્રિલિંગ પ્રક્રિયા તથા એના ટૂલિંગ સંબંધી જાણકારી મેળવીશું. ડ્રિલિંગ કરતી વખતે કઈ ભૂલો સંભવ છે, એ ભૂલોની બોઅરિંગ પર થનારી અસર તથા સામાન્ય ડ્રિલિંગ કરતી વખતે જેનો સામનો કરવો પડતો હોય છે, તે મુશ્કેલીઓ વિશે આપણે આ લેખમાં માહિતી મેળવીશું.
ડ્રિલ (ખાસ કરીને ઇન્સર્ટ અથવા ઈન્ડેકસેબલ) ડિઝાઇન કરતી વખતે નીચે આપેલી પ્રાથમિક બાબતો ચકાસવી જરૂરી હોય છે.
સ્પિન્ડલ
મશીનમાં ‘થ્રૂ કૂલંટ સ્પિન્ડલ’ છે કે સામાન્ય સ્પિન્ડલ છે, એ ચકાસવું અત્યંત જરૂરી છે. જો લંબાઈ તથા વ્યાસનો ગુણોત્તર (L/D), 5 અથવા એનાથી વધુ હોય અને મટિરિયલની આંતરિક સ્ટ્રેન્થ વધુ હોય તો ‘થ્રૂ કૂલંટ સ્પિન્ડલ’ નો ઉપયોગ જરૂરી છે. ઍલ્યુમિનિયમ, કાસ્ટ આયર્નના યંત્રણ માટે થ્રૂ કૂલંટ સ્પિન્ડલની જરૂરત નથી હોતી. પણ સ્ટીલ, સ્ટેનલેસ સ્ટીલના યંત્રણ વખતે થ્રૂ કૂલંટ સ્પિન્ડલનો ઉપયોગ, યંત્રણની ઉત્પાદકતા વધારી શકે છે અને ઉત્પાદનનો ખર્ચો ઘટાડી શકે છે.
ડ્રિલિંગ કરવાનું હોય તે સપાટીનું સ્વરૂપ
ઇન્સર્ટ પ્રકારનું ડ્રિલ ડિઝાઈન કરતી વખતે, પાર્ટની સપાટી અંતર્ગોળ (કૉન્કેવ) છે કે બહિર્ગોળ (કૉન્વેક્સ) છે, એ જાણવું જરૂરી છે. ડ્રિલના મુખ પર કેન્દ્રમાં (સેન્ટર) માં એક ઇન્સર્ટ હોય છે તથા એક પેરીફેરલ ઇન્સર્ટ (ચિત્ર ક્ર. 1) હોય છે. ડ્રિલિંગ દરમિયાન પ્રથમ તો કેન્દ્રમાં સ્થિત ઇન્સર્ટનો સંપર્ક પાર્ટ સાથે થાય એ અપેક્ષા રાખવામાં આવે છે. ઇન્સર્ટનો સંપર્ક પાર્ટ સાથે થતા, એનો સંદર્ભ લઈ યંત્રણ શરૂ થાય છે. સપાટી જો બહિર્મુખ હોય, તો કેન્દ્રમાં સ્થિત ઇન્સર્ટનો પહેલો સંપર્ક થાય છે, પણ જો સપાટી અંતર્મુખ હોય તો યંત્રણ દરમિયાન પેરીફેરલ ઇન્સર્ટ પ્રથમ સંપર્કમાં આવે છે. પેરીફેરલ ઇન્સર્ટનો સંપર્ક પહેલા થવાથી ટૂલનો અક્ષ ખસે છે. અક્ષ સ્થાનાંતરિત થવાના કારણે, યંત્રણ શરૂ થતા પહેલા જ વ્યાસનું ડીસ્ટોર્શન થવાનું સંભવ છે. એનાથી અપેક્ષિત વ્યાસ પ્રાપ્ત નથી થતો. ઇન્સર્ટ તૂટી જાય છે. એટલા માટે એ અગાઉ ચકાસવું જરૂરી છે, કે પાર્ટની સપાટી અંતર્મુખ છે કે બહિર્મુખ. કાસ્ટિંગ પ્રક્રિયાથી બનેલ કાર્યવસ્તુમાં જો છિદ્ર હોય, તો ત્યાં કોર ડ્રિલ અથવા ફ્લૅટ સેન્ટર સ્પૉટ ફેસ કરવામાં આવે છે.
મશીનની ક્ષમતા
મશીન અપેક્ષિત ક્ષમતાનું છે કે નહીં, તે ચકાસવું જરૂરી છે. ડ્રિલિંગના વ્યાસ પર ઘણી બાબતો નિર્ભર કરે છે. ઈન્ડેકસેબલ ડ્રિલમાં 12.5 મિમી. થી વધુ વ્યાસ માટે ઇન્સર્ટ પ્રકારના ડ્રિલનો ઉપયોગ કરી શકાય છે. 12.3 મિમી. થી ઓછા વ્યાસનું ડ્રિલિંગ કરવું હોય, તો એચ.એસ.એસ. અથવા કાર્બાઈડ સ્ટીલના ડ્રિલનો ઉપયોગ કરવામાં આવે છે. 12.3 મિમી. થી વધુ વ્યાસનું ડ્રિલ ઈન્ડેકસેબલ ટૂલથી કરવું હોય તો, ડ્રિલના વ્યાસ અનુસાર પર્યાપ્ત હૉર્સપાવરના મશીનની પસંદગી કરવામાં આવે છે. આગળ આપવામાં આવેલ સમીકરણથી, મશીનની જરૂરી શક્તિ જાણી શકાય છે.
જરૂરી શક્તિવાળું મશીન ઉપલબ્ધ ન હોય, તો યંત્રણ કરતી વખતે ટૂલ એક ચોક્કસ ઊંડાઈ સુધી પહોંચે છે અને અપૂરતી શક્તિને કારણે સ્પિન્ડલ અટકી જાય છે. એનાથી ડ્રિલ ટૂટી શકે છે. યંત્રણની જરૂરિયાત અનુસાર, અલગ અલગ સ્પિન્ડલ શક્તિવાળા મશીન ઉપલબ્ધ છે.
મટિરિયલ
પાર્ટનું મટિરિયલ કયું છે એ જોવું પણ અત્યંત મહત્ત્વપૂર્ણ છે. કેમકે જો એલ્યુમિનિયમ પાર્ટનો L/D ગુણોત્તર 5 થી વધુ હોય, તો પણ ટૂલ ઉત્પાદક એ જોખમ લઈ શકે છે, પણ સ્ટીલ પાર્ટમાં ગુણોત્તર 5 થી વધુ ન હોવો જોઈએ. એનાથી વધુ ગુણોત્તરમાં ડ્રિલ કરવા માટે ડૅમ્પ કરેલ ઍડાપ્ટર (ચિત્ર ક્ર. 2) નો ઉપયોગ કરવો પડે છે. પણ ડૅમ્પ કરેલ ઍડાપ્ટરમાં સ્પિન્ડલની અંદરથી કૂલંટ આપવું સંભવ નથી.
ટૂલની રચના
સ્ટીલની બૉડીમાં બેસાડવામાં આવેલ અમારા કાર્બાઈડ ઇન્સર્ટ સુધી શીતક બે પ્રકારે પહોંચાડવામાં આવે છે. ડૅમ્પ કરેલ બોઅરિંગ બારને શીતક આપી શકાતું નથી. આ સમસ્યાથી બચવા માટે કાર્બાઈડ રૉડ પર 2 સ્ક્વેઅર સ્લૉટ બનાવવામાં આવે છે. કાર્બાઈડ રૉડની બહાર ડ્રિલ બૉડી હોય છે. બૉડીમાં પાછળથી છિદ્ર કરી એમાં કાર્બાઈડ રૉડ નાખવામાં આવે છે. કાર્બાઈડ રૉડ માટે સેન્ટર થ્રૂ કૂલંટવાળો સ્ટૅન્ડર્ડ કાર્બાઈડ રૉડ ઉપયોગમાં લેવાય છે.
• આમાં વચ્ચોવચ એક છિદ્ર હોય છે.
• એનો વ્યાસ ઓછો હોય તો શીતકનો પ્રવાહ પણ ઓછો થાય છે. એ પ્રવાહની માત્રા યોગ્ય હોવી જરૂરી છે. તેની ગણતરી લીટર પ્રતિ મિનિટમાં કરવામાં આવે.
• શીતકને જો ઇન્સર્ટની ટિપ સુધી પહોંચાડવાનો હોય, તો આ સ્થાન પર વાયરકટ અથવા ઈ.ડી.એમ. પ્રક્રિયાથી ખાંચો બનાવવામાં આવે છે.
• ખાંચો બનાવ્યા પછી શીતક કેન્દ્રમાં નથી રહેતું. એનાથી શીતકનો ઉચિત પ્રવાહ પ્રાપ્ત થાય છે તથા થ્રૂ કૂલંટનું કામ યોગ્ય થાય છે. આનો ઉપયોગ ડ્રિલિંગ માટે કરવામાં આવે છે. સાથે જ સેમિફિનિશ તથા ફિનિશ બોઅરિંગમાં પણ એનો ઉપયોગ કરવામાં આવે છે.
ડ્રિલિંગને બોઅરિંગનું પ્રથમ ચરણ માનવામાં આવે છે. ફ્લૅટ સપાટીથી આપણે જો 40 ± 0.02 માયક્રૉન ફિનિશ બોઅરિંગ કરવું હોય, તો ફિનિશ બોઅર માટે 0.5 મિમી. વ્યાસથી વધુ અલાઉન્સ ન હોવું જોઈએ. એનાથી 39.5 મિમી. વ્યાસ પર સેમીફિનિશિંગ હોવું અપેક્ષિત હોય છે. ધારો કે 5 હૉર્સપાવર ક્ષમતાવાળા મશીન પર 38 મિમી. નું ડ્રિલિંગ કરવું છે. મશીનની ક્ષમતા અપૂરતી હોવાને કારણે 25 મિમી. નો ડ્રિલ જ સંભવ હોય છે. એટલે પ્રથમ 25 મિમી. નો ડ્રિલ કરો, પછી જ કોર ડ્રિલનો ઉપયોગ કરો. કોર ડ્રિલના ઉપયોગથી 38 મિમી. વ્યાસ પ્રાપ્ત કરો. સેમીફિનિશ કરતી વખતે આ વ્યાસ 39.5 મિમી. કરો. એના પછી જ આપને ફિનિશ બોઅરમાં અપેક્ષિત વ્યાસ પ્રાપ્ત થશે.
અપેક્ષિત ઉત્પાદન
આઉટપુટ કેટલી ક્ષમતાથી હોવું જોઈએ, તે પણ એટલું જ મહત્ત્વપૂર્ણ છે. ઉચ્ચ પૅરામીટરનો ઉપયોગ કરવો હોય, તો ચિપનો નિકાસ કેવી રીતે કરવો, એ વિશે વિચારવું પડે છે. ડ્રિલ બનાવતી વખતે ચિપના પ્રવાહ માટે ફલ્યૂટને સુપર ફિનિશ એટલે બફિંગ કરવામાં આવે છે. તેમ છતાં પણ ફલ્યૂટ હજી વધારે ફિનિશ તો કરવા જ પડે છે. જેટલું સારું ફિનિશિંગ હશે એટલો જ ચિપનો પ્રવાહ સારો થશે. ચિપનો પ્રવાહ સારો ન હોય, તો યંત્રણ પૅરામીટર પર અસર પડે છે. શીતકનું દબાણ ઓછામાં ઓછું 16 બાર હોવું જરૂરી છે. શીતકનું દબાણ યોગ્ય ન હોય, તો ચિપના નિકાસમાં મુશ્કેલી આવી શકે છે.
ટૂલની પસંદગી
ઇન્સર્ટની પસંદગી પણ એક મહત્ત્વપૂર્ણ નિર્ણય ગણાય છે. ઇન્સર્ટની પસંદગી કાર્યવસ્તુના મટિરિયલ પર નિર્ભર કરે છે. સિંગલ ડ્રિલના નિર્દેશ, મલ્ટિસ્પિન્ડલ ડ્રિલિંગ અથવા ગઁગ ડ્રિલિંગના નિર્દેશોથી અલગ હોય છે. ગઁગ ડ્રિલિંગના તથા મલ્ટિસ્પિન્ડલ ડ્રિલિંગ માટે ઈન્ડેકસેબલ ડ્રિલનો ઉપયોગ નથી કરવામાં આવતો, કેમકે મલ્ટિસ્પિન્ડલ માટે ડ્રિલનો વ્યાસ 12 મિમી. થી ઓછો હોય છે. એક સમયે એક થી વધુ છિદ્રો કરવા હોય, તો એના માટે ઘણી વધુ શક્તિ જરૂરી હોય છે.
આ વિશે આપણે વધુ ઊંડાણપૂર્વક જાણીએ. ઈન્ડેકસેબલ ડ્રિલ (ચિત્ર ક્ર. 3) તથા સામાન્ય એચ.એસ.એસ. અથવા કાર્બાઈડ ડ્રિલનું (કોષ્ટક ક્ર. 1) પ્રથમ વર્ગીકરણ યંત્રણ ગતિ પર નિર્ભર હોય છે. એચ.એસ.એસ. માં 12, 15, 20 મીટર/મિનિટની યંત્રણ ગતિ પ્રાપ્ત થાય છે. એચ.એસ.એસ. ના M35, M42 આ પ્રકારોમાં યંત્રણ ગતિ 15, 20, 25 ટકા સુધી વધશે. કાર્બાઈડના ઉપયોગથી પણ 50 થી 70 મીટર/મિનિટ સુધીની ગતિ પ્રાપ્ત થાય છે. ઈન્ડેકસેબલમાં આ ગતિ 100 મીટર/મિનિટથી શરુ થાય છે. આ ડ્રિલ માટે ન્યૂનતમ 100 થી વધુમાં વધુ 400 મીટર/મિનિટની યંત્રણ ગતિ જરૂરી હોય છે. આ તમામ બાબતોને ધ્યાનમાં રાખીને મટિરિયલ તથા અન્ય બાબતોનો ઉપયોગ કરવામાં આવે, તો યંત્રણ સમય (મશીનિંગ સમય) ત્રણ થી ચાર ગણો ઘટી શકે છે. આ સંદર્ભે મશીનની શક્તિ ઉચિત હોવી જરૂરી છે.
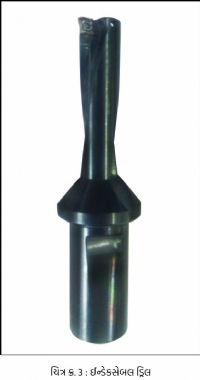
ઈન્ડેકસેબલ ડ્રિલમાં રીશાર્પનિંગ નથી થતું, માત્ર ઇન્સર્ટનું ઇન્ડેક્સિંગ થાય છે. એચ.એસ.એસ. નો ઉપયોગ કરવો હોય, તો ટૂલ કિટમાં વધુ સંખ્યામાં ડ્રિલ રાખવા પડે છે. એમનું રીશાર્પનિંગ નક્કી કરેલ સમય પર કરવું જરૂરી હોય છે. એનાથી ઇન્વેન્ટરી વધે છે. પણ કાર્બાઈડ ડ્રિલમાં આની જરૂરિયાત નથી હોતી, એક ડ્રિલ મશીન પર તો એક જ ડ્રિલ સ્ટૉકમાં હોય છે.
ઈન્ડેકસેબલ ડ્રિલની જે ધારો મટિરિયલના સંપર્કમાં આવે છે, એ જ ધારો દ્વારા યંત્રણ કરવામાં આવે છે. સૉલિડ કાર્બાઈડ અથવા એચ.એસ.એસ. ડ્રિલના ફલ્યૂટની ધારો વિશેષ રીતે તૈયાર કરવામાં આવે છે. ઈન્ડેકસેબલ ઇન્સર્ટમાં માત્ર પૉઈન્ટ દ્વારા યંત્રણ કરવામાં આવે છે. ઈન્ડેકસેબલમાં 56 મિમી. વ્યાસ સુધી 2 ઇન્સર્ટનો ઉપયોગ કરવામાં આવે છે. વ્યાસ જો 56 મિમી. થી વધુ હોય તો 3 ઇન્સર્ટનો ઉપયોગ કરી શકાય છે. એનાથી વધુ ઇન્સર્ટનો ઉપયોગ શક્ય નથી કેમકે 56 મિમી. નું ડ્રિલ કરવા યોગ્ય ક્ષમતા (70 HP) નું મશીન હોવું જરૂરી છે. જ્યારે 56 મિમી. થી વધુ વ્યાસનું કામ હોય, ત્યારે લગભગ 3 ઇન્સર્ટ ઉપયોગમાં લેવાય છે. આ સ્થિતિમાં એક ઇન્સર્ટ વચમાં તથા બે ઇન્સર્ટ પેરિફરલ પર હોય છે. 4 ઇન્સર્ટ પણ લગાડી શકાય છે, પણ એના માટે બીજી ડિઝાઇનનો ઉપયોગ કરવામાં આવે છે. કેમકે 76 મિમી. ના વ્યાસ માટે વધુ મટિરિયલ કાઢવું પડે છે, ટૂલમાં માત્ર ઇન્સર્ટ લગાડવાને બદલે કાર્ટ્રિજ (ચિત્ર ક્ર. 4) લગાડી શકાય છે. આ પ્રકારમાં કાર્ટ્રિજમાં ઇન્સર્ટ બેસાડવામાં આવે છે. સેંટર કટિંગમાં એક, બાજૂમાં એક અને પેરિફેરલમાં એક, એમ કુલ 3 કાર્ટ્રિજ હોઈ શકે છે. જો ઇન્સર્ટ ખરાબ થાય તો માત્ર કાર્ટ્રિજ જ ફેંકવું પડે છે, આખી બૉડી નકામી નથી થઈ જતી. બાકી, સામાન્ય ડ્રિલમાં ઇન્સર્ટ ખરાબ થાય અથવા તૂટી જાય તો ડ્રિલનો આકાર બગડી જાય છે. એ કારણે પૂર્ણ બૉડી ફેંકી દેવી પડે છે. મોટા વ્યાસના કામ માટે સામાન્ય ડ્રિલને બદલે કાર્ટ્રિજનો ઉપયોગ અત્યંત સુવિધાજનક સાબિત થાય છે.
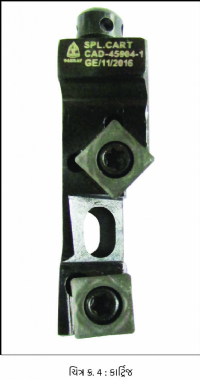
કાર્ટ્રિજથી ડ્રિલની બૉડી ઘણો લાંબો સમય ચાલી શકે છે. બૉડીની હાર્ડનેસ યોગ્ય હોવી જોઈએ, એ વધુ કઠણ હોય તો ટિપ/યંત્રણ બિંદુ (કટિંગ પોઈન્ટ) પર ભાર (લોડ) આવે છે. આ ભાર બૉડી પર લાગુ પડે છે. બૉડી પર ભાર વધવાથી ઘસારો વધે છે તથા પૉકેટ ડીફોર્મ થાય છે. 2, 3 અથવા 5 પાર્ટ પછી આકારમાં સાતત્યતા ન મળવાથી યંત્રણ કાર્ય અટકાવી દેવું પડે છે. હાર્ડનેસ 50 HRC થી વધુ થઈ જાય તો બૉડી એ ભાર સહન નથી કરી શકતી. એનાથી કંપનો/ધ્રુજારી તથા ચૅટર ઉદ્દભવે છે. એટલા માટે બૉડીની હાર્ડનેસ 40-48 HRC વચ્ચે હોવી જરૂરી છે. હાર્ડનેસ 40 HRC થી ઓછી થાય તો ડ્રિલ વધુ લાંબો સમય નથી ચાલતી. એટલા માટે N19, N24 એટલે ઍલૉય સ્ટીલ મટિરિયલ ઉપયોગમાં લેવાય છે. N47 નો ઉપયોગ પણ કરવામાં આવે છે, જે સ્પ્રિંગ સ્ટીલ હોય છે. એમાં થોડી માત્રામાં સિલિકૉન હોવાને કારણે, એ સ્પ્રિંગની જેમ સ્થિતિસ્થાપક હોય છે. ટૉર્શન સ્ટ્રેન્થ પણ સારી હોય છે. એટલા માટે રોટેટિંગ ટૂલ માટે N47 મટિરિયલની ભલામણ કરવામાં આવે છે. કેટલાક મટિરિયલની હાર્ડનેસ 40-44 HRC ની વચ્ચે હોય છે. એના માટે P20 મટિરિયલનો ઉપયોગ કરવાથી P20 ને 48 HRC સુધીની કઠોરતા મળે છે. હાર્ડનેસ જ્યારે 45 HRC થી વધુ હોય, ત્યારે યંત્રણ ક્ષમતા ખૂબ ઓછી હોય છે. એ કારણે હાર્ડનિંગ પછી જ પૉકેટિંગ કરવું યોગ્ય હોય છે.
નાના વર્કશોપમાં ઇન્સર્ટને પણ રીશાર્પનિંગ કરવામાં આવે છે.રીશાર્પનિંગ કરવામાં આવેલ ઇન્સર્ટનો ઉપયોગ ડ્રિલિંગ માટે કરવામાં નથી આવતો કેમકે રીશાર્પનિંગ કરતી વખતે એમની ભૂમિતિ જાળવી રાખવા બાબતે ધ્યાન રાખવામાં નથી આવતું. ફળસ્વરૂપે ઇન્સર્ટનો આકાર નાનો થાય છે, જેનાથી ઑફસેટ પણ ઓછો થાય છે. રીશાર્પનિંગ થયા બાદ ઇન્સર્ટની સેન્ટર હાઈટની કોઈ ગૅરંટી નથી હોતી. એટલા માટે એનો ડ્રિલિંગમાં ઉપયોગ નથી કરી શકાતો.
ગિરીશ ફડકે, મેકૅનિકલ એન્જિનિયર છે. આપે 6 વર્ષ ટાટા મોટર્સમાં કામ કર્યું છે. છેલ્લા 26 વર્ષથી આપ ઔરંગાબાદ સ્થિત ગૌરવ એન્જિનિયર્સના ડાયરેક્ટર છો.
9225641450