1990 સુધી, મોટી કંપનીઓની પાસે તેમના પોતાના ટૂલ રૂમ હતા. આ ટૂલ રૂમમાં એ કંપનીઓની પોતાની ઉત્પાદન પ્રક્રિયા (મૅન્યુફૅક્ચરિંગ પ્રોસેસ) માટે જરૂરી ‘જીગ્સ અને ફિક્શ્ચર્સ’ અથવા નાની નાની ‘એસ.પી.એમ.’ જાતે જ ડિઝાઈન કરીને બનાવવામાં આવતી હતી. થોડા અનુભવ પછી એમને એ વાતનો ખ્યાલ આવ્યો કે ટૂલ રૂમમાં થતું કાર્ય સરવાળે મોંઘું પડતું હતું અને એજ કારણે દરેક કંપનીઓએ પોત પોતાની પૉલિસીમાં બદલાવ કરી આ કાર્ય અન્ય બાહરી પુરવઠાકારો (સપ્લાયરો)પાસેથી કરાવવાની શરૂઆત કરી. અમને એક પુરવઠાકાર તરીકે હંમેશા પડકારરૂપ કાર્યો કરવાની તક મળતી ગઈ અને ‘એ.એસ.આર.’ની યાત્રા આમાંથી જ શરુ થઇ.
વી.એમ.સી. પર કૅમશાફ્ટનું ડ્રિલિંગ કરવા માટે ફિક્શ્ચર
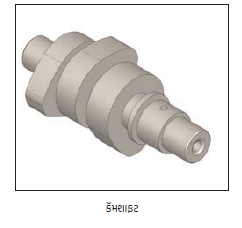
ઑટોમાબાઈલ ઉદ્યોગના અમારા એક નિયમિત ગ્રાહક દ્વારા અમને વી.એમ.સી. પર એક કૅમશાફટ માટે 4 મિમી. વ્યાસનું છિદ્ર બનાવવાના માટેના ફિક્શ્ચર અંગે પૂછવામાં આવ્યું. આ છિદ્ર અત્યંત મહત્ત્વપૂર્ણ હતું કારણ કે એમાંથી એન્જિન માટેના ઊંજણ તેલનો (લુબ્રિકન્ટ) પુરવઠો કરવાની સાથે, મશિનિંગ ઑપરેશનના આગલા તબક્કા માટે એનો ઉપયોગ લોકેશન તરીકે કરવાનો હતો. એ કારણે આ છિદ્રના ચોક્કસ પરિમાણો તથા એનો અક્ષ અને ઇનલેટ કૅમની ફોર્જિંગની સ્થિતિમાં બનતી પ્રોફાઈલ, એ બંનેનો પરસ્પર સંબંધ (ઇન્ટરરિલેશન) અત્યંત અચૂક સ્તરે (±2°) હોવો જરૂરી હતો (ચિત્ર ક્ર. 1). ઉત્તમ ગુણવત્તાનું કૅમશાફટ બનાવવા માટે ફિક્શ્ચર બનાવવાની રૂપરેખામાં અમે કૅમશાફટના સેમિફિનિશ ટર્નિંગ કરવામાં આવેલ બંને જર્નલ વ્યાસ (ડાયામીટર) અને ફોર્જિંગની સ્થિતિમાં ઇનલેટ કૅમની પ્રોફાઈલ એના સંદર્ભો લીધા (ચિત્ર ક્ર. 2). પણ એમાં સૌથી મોટી સમસ્યા એ હતી કે જર્નલ વ્યાસના ટૉલરન્સ અને કૅમના ટૉલરન્સમાં ઘણો ફર્ક હતો. પરિણામે કૅમશાફટ ફિક્શ્ચર પર કસીને બેસી જાય એ પછી, બન્ને જર્નલમાંથી એક અથવા ઇનલેટ કૅમ પ્રોફાઈલની સપાટીમાં જગ્યા (ગૅપ) દેખાવા લાગી.
અધૂરામાં પૂરું, દરેક કાર્યવસ્તુ માટે અલગ અલગ જગ્યા દેખાતી હતી. એ કારણે આગળના ઑપરેશનમાં રિજેકશનની સમસ્યા ઉભી થઈ. આ સમસ્યા પર ઉપાય શોધવા માટે ઇનલેટ કૅમ પ્રોફાઈલ સરખી રીતે બેસાડવા માટે આપેલ ‘V’ એક જ જગ્યા પર સ્થિર કરવાને બદલે સ્પ્રિંગ લોડેડ કરવામાં આવ્યો. આમ કરવાથી કાર્યવસ્તુના બન્ને જર્નલ વ્યાસ V બ્લૉક પર સરખી રીતે બેસી ગયા બાદ, ઇનલેટ કૅમ પ્રોફાઈલ લગાડતી વખતે એના માપમાં જો કોઈ ફેર હોય તો, સ્પ્રિંગના દબાણને કારણે આપમેળે જ ઍડજસ્ટ થઇ જતો હતો. તેથી કાર્યવસ્તુને જોઇયે ત્યાં એટલે યોગ્ય સ્થાન પર રાખવાનું સરળ થઇ ગયું. અક્ષીય સ્થાન નિશ્ચિત કરવાની વ્યવસ્થા પણ કરવામાં આવી. આમ આ દોષરહિત વિકલ્પને કારણે આગળનું સંભવિત રિજેકશન પણ ટાળી શકાયું. આ ગોઠવણ ચિત્ર ક્ર. 3 માં દર્શાવવામાં આવી છે.
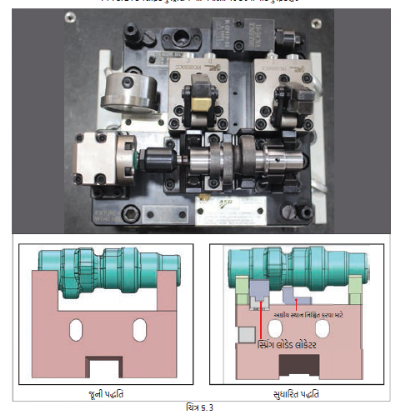
સૌ પ્રથમ અમે કમ્પ્યુટર પર એનું એક કાલ્પનિક ચિત્ર તૈયાર કર્યું. ગ્રાહકની મંજૂરી લીધી અને તરત જ એ ફિક્શ્ચર બનાવી દીધું. સફળ પરીક્ષણો પછી એ ફિક્શ્ચરને ગ્રાહકના કારખાનામાં બેસાડી સક્રિય કરવામાં આવ્યું. બધું વ્યવસ્થિત ચાલી રહ્યું હતું પણ અચાનક એક દિવસ કૅમશાફટનો પૂરો બેચ જ રિજેક્ટ થઇ ગયો. કૅમના લોબનું મશીનિંગ (યંત્રણ) કરતી વખતે ફોર્જિંગના ડાઘ દેખાવા લાગ્યા. ઉત્પાદનમાં કટોકટીની સ્થિતિ સર્જાઈ અને બધા ચિંતિત થઇ ગયા. શરૂઆતમાં સૌને ફિક્શ્ચરની ચોકસાઈ અંગે શંકા હતી. પણ ફિક્શ્ચરની તપાસ અને પરીક્ષણ કર્યા બાદ કોઈ ખામી નથી એમ જણાયું. એ સમયે મેં જાતે ગ્રાહકના કારખાનામાં જઈ સમસ્યાનું ઊંડાણપૂર્વક વિશ્લેષણ કર્યું. ત્યાંની તમામ પ્રક્રિયાઓનો, એમની ટીમ સાથે ઉંડાણપૂર્વકનો અભ્યાસ કર્યા બાદ સમસ્યાનું મૂળ પકડાયું. તે હતું અગાઉ કરવામાં આવેલ સેંટરિંગનું કામ. એ ખામી દૂર કરતાની સાથે જ સમસ્યાનું નિવારણ થઇ ગયું.
ગોળ આકારના જર્નલ વ્યાસના લગભગ કેન્દ્ર પર સેંટરિંગ ઑપરેશન કરી શકાય, એવું માનીને કામ કરવામાં આવતું હતું. એની અંદર કૅમના લોબનો કોઈ પણ કોણીય સંદર્ભ (અઁગ્યુલર રેફરન્સ) લેવામાં આવ્યો ન હતો. ઓછી યંત્રણ છૂટ (મશીનિંગ અલાઉન્સ) વાળા ભાગ તરફ જ્યારે સેન્ટર સરકતું હતું, ત્યારે પછીના ઑપરેશનમાં ફોર્જિંગના ડાઘ રહી જતા હતા. સેંટરિંગ ઑપરેશનના ફિક્શ્ચરમાં કૅમના લોબનો કોણીય સંદર્ભ લઇ એ સમસ્યાનું નિવારણ કરવામાં આવ્યું. ગ્રાહકની સમસ્યાને પોતાની સમસ્યા માનીને તેને હલ કરવાની અમારી પરંપરા રહી છે. અમે અમારા કારખાનામાં શરૂઆતથી જ કેટલાક સિદ્ધાંતોનું પાલન કરી રહ્યા છીએ. અમારા ઘણાં ખરા ઑપરેટર અલ્પશિક્ષિત છે પણ કામની ગુણવત્તાને તેઓ પોતાની જવાબદારી સમજે છે.
1. એવી વ્યવસ્થા કરવી જોઈએ જેમાં માનવીય શ્રમ ન્યૂનતમ હોય.
અમારા સેટ અપને વિશ્વ સ્તરીય (વર્લ્ડ ક્લાસ) બનાવવાની કોશિશો નિરંતર ચાલતી રહે છે. દાખલા તરીકે,
• ઉત્પાદન વિભાગ માટે આધુનિક સી.એન.સી. મશીન અને પરીક્ષણ માટે સી.એમ.એમ.
• ડિઝાઈન વિભાગ માટે અત્યાધુનિક સંગણક અને એના માટે જરૂરી 3D સોફ્ટવેર
• દરેક ડિઝાઈનનું સિમ્યુલેશન કરવામાં આવે છે
• સ્વચ્છ અને સુઘડ લેઆઉટ
• સ્વ-શિસ્ત અને કાર્ય કરવાની વિશેષ શૈલી
2. દરેક કાર્યપદ્ધતિનો ઊંડાણપૂર્વક અભ્યાસ કરી, તેની અંદરના તમામ જરૂરી કાર્યો દર્શાવનાર કોષ્ટકો તૈયાર કરી કામની જગ્યાએ લગાડ્યા. એનું ફળ એ આવ્યું કે રોજના કામ દરમિયાન કોઈ પણ કાર્ય ભૂલવાની સંભાવનાઓ ખતમ થઇ ગઈ અને જો ધારો કે ભુલાઈ પણ ગઈ તો એને ન્યૂનતમ સમયમાં તેમ જ ઓછી મહેનત દ્વારા સુધારી શકાય છે. ફ્લો ચાર્ટ જોઇને પણ આખી પ્રક્રિયા સમજી શકાય છે. સંદર્ભ માટે કોષ્ટક ક્ર. 1 જૂઓ.
3. કામમાં માનવીય ભૂલો નહિવત રાખવા માટે આધુનિક ટેક્નૉલૉજીનો ઉપયોગ
• રોજીંદા કામકાજમાં કાગળ વિનાની પદ્ધતિ (પેપરલેસ વર્કિંગ)
• દરેક ડ્રૉઈંગ તથા ડિઝાઈન કમ્યુટર પ્રોગ્રામ દ્વારા જ તૈયાર કરવામાં આવે છે.
• દરેક મહત્ત્વપૂર્ણ માહિતી સર્વર પર જાળવવામાં (સેવ્હ કરવામાં) આવે છે.
• દરેક કર્મચારીને એમના કાર્ય સાથે સંબંધિત કાર્યવસ્તુ તથા અસેમ્બ્લીના ડ્રૉઈંગ, એમના કાર્યસ્થળની પાસે જ સંગણક પર ઉપલબ્ધ કરાય છે.
• દરેક તબક્કે દરેક કાર્યવસ્તુના, કયા કયા પેરામીટર પર તપાસવામાં આવશે એનું એક તૈયાર ચેકલિસ્ટ બનાવી સંગણક પર એક ચોક્કસ ફૉર્મેટમાં આપેલું હોય છે.
• આપવામાં આવેલ ચેકલિસ્ટ અનુસાર દરેક કાર્યવસ્તુની, જે તે તબક્કે તપાસ કરી એ તમામ માહિતી સંગણક પર જ અન્ય ફૉર્મેટમાં પ્રવિષ્ટ કરવાની વ્યવસ્થા કરવી.
• સંગણકમાં પ્રવિષ્ટ કરવામાં આવેલ આ માહિતી કોઈ પણ કર્મચારી ગમે ત્યારે જોઈ શકે છે પણ એમાં એ કોઈ ફેરફાર નથી કરી શકતા.
• આ કાર્યપદ્ધતિ અપનાવાથી, કામમાં કોઈ રીવર્ક અથવા કોઈ રિજેકશન આવવાની શકયતા નહિવત હોય છે અને મોટાભાગે અચૂક પરિણામો મળે છે. આથી બિનજરૂરી ખર્ચો પણ ટાળી શકાય છે.
4. ગ્રાહક માટે બનાવેલ કોઈ પણ ફિક્શ્ચર તેનું અંતિમ પરીક્ષણ કર્યા પછી જ ગ્રાહક પાસે મોકલવું.
5. કોટેશનના સંદર્ભે ગ્રાહક સાથે રાખવામાં આવેલ સંપૂર્ણ પારદર્શિતા
અમારી સૌથી મોટી ખાસિયત એ છે અમારો કોઈ અલગ વિપણન (માર્કેટિંગ) વિભાગ નથી. ઉપર વર્ણવેલ તમામ વિશ્વસ્તરીય પ્રણાલીઓદ્વારા માર્કેટિંગનું કામ આપમેળે જ થતું રહે છે. પણ એનો અર્થ એ નથી કે ગ્રાહકો સાથે સંવાદ સાધનાર અમારો બીજો કોઈ વિભાગ જ નથી. ગ્રાહકોની જરૂરીયાત ઓળખવાની અમારી એક સરળ રીત છે. કોઈ પણ ગ્રાહક જ્યારે ફિક્શ્ચર વિશે પૂછપરછ કરે ત્યારે અમારી એમને સ્પષ્ટ વિનંતી હોય છે કે એ પોતાના પાર્ટની પૂર્ણ માહિતી મેળવીને, પૂર્ણ અભ્યાસ કરીને જ આવે. અમે એ ગ્રાહક પાસેથી એ પાર્ટ વિશેની તમામ માહિતી અમે તૈયાર કરેલ વિશેષ ફોર્મમાં ભરીએ છીએ. આ જાણકારી એટલે બંને પક્ષો દ્વારા સ્વીકૃત પ્રાથમિક તબક્કો ગણવામાં આવે છે. ત્યાર બાદ જ આગળના કાર્યની શરૂઆત થાય છે. ત્યાર પછી વેચાણપશ્ચાત સેવા, એટલે એ ફિક્શ્ચરને સફળતાપૂર્વક કાર્યાન્વિત કરવાની પ્રક્રિયા, માત્ર એક ઔપચારિકતા જ હોય છે. હવે આપણે એક ઉદાહરણ જોઇ લિયે.
ડિઝલ એન્જિનના ‘ઑઈલ પૅન’ માટે એચ.એમ.સી. પર બેસાડવાનું ફિક્શ્ચર
ડિઝલ એન્જિનનું ઉત્પાદન કરનાર એક પ્રખ્યાત ઉદ્યોગ દ્વારા એમના ઑઈલ પૅનનું સંપૂર્ણ યંત્રણ એચ.એમ.સી. પર કરવા માટે ઉચિત ફિક્શ્ચર બનાવવા માટે અમને પૂછવામાં આવ્યું. ઍલ્યુમિનિયમ જેવી ધાતુમાંથી બનેલ આ પાર્ટ વજનમાં હલકો તો હતો જ પણ સાથે સાથે પાતળો તથા આકારમાં અંતર્ગોળ પણ હતો. એની આવી વિશિષ્ટ રચનાને કારણે, તેના યંત્રણ સમયે જો એ જરા પણ વધુ કસીને પકડાઈ જાય તો એનો આકાર બદલાઈ જતો હતો, જેથી એની ગુણવત્તા બગડતી હતી, એ મોટામાં મોટી મુશ્કેલી હતી. એમાં સુસંગતતા પણ જળવાતી ન હતી. જો કાર્યવસ્તુ ઓછી તાકાતથી પકડવામાં આવે તો ઉત્પાદન કરવા માટે વધુ સમય લાગતો હતો અને ઉત્પાદકતા પણ ઘટી જતી હતી. એ ઉપરાંત યંત્રણ કરતી વખતે એક સાથે દબાણ વધી ન જાય એ માટે પ્રક્રિયા વિભાજીત કરવી પડી, જે કારણે યંત્રણ માટેનો સમય પણ વધી રહ્યો હતો. ફળસ્વરૂપ, ગ્રાહક માટે અપેક્ષિત ગુણવત્તા, કિંમત તથા વિશ્વસનીય પુરવઠો પૂરો પાડવાનું મુશ્કેલ થઇ રહ્યું હતું.
આ પડકારનો સ્વીકાર કરીને અમે બધા પાસાઓનો વિચાર કરીને એક ઉત્તમ ફિક્શ્ચર બનાવી આપ્યું. આ ફિક્શ્ચર બનાવવા માટે ઑઈલ પૅનને માત્ર બે સેટઅપમાં બનાવાનો પ્રસ્તાવ અમે મૂક્યો. આ સેટઅપમાં નીચેની સુવિધાઓ શામેલ કરવામાં આવી હતી.
અ. કાર્યવસ્તુને પકડવામાં એકરૂપતા અને સુસંગતતા પ્રાપ્ત કરવાના હેતુથી બંને સેટઅપમાં કાર્યવસ્તુ હાઈડ્રોલિક પદ્ધતિથી પકડવાની વ્યવસ્થા કરવામાં આવી.
બ. પ્રથમ સેટઅપમાં નિર્ધારિત ઑપરેશન હતાં - ઑઈલ પૅનના બ્લૉક પરની સપાટીનું મિલિંગ, એનો ખાંચો (ગ્રુવ), પછીના ઑપરેશનના સંદર્ભ માટે છિદ્ર (રેફરન્સ હોલ) તથા બોલ્ટ માટે અન્ય છિદ્રો (માઉન્ટિંગ હોલ). સામાન્ય રીતે કોઈ પણ મિલિંગ ઑપરેશન કરતી વખતે કાર્યવસ્તુને મશીનના સ્પિન્ડલની વિરુદ્ધ દિશામાં ખેંચીને બેસાડવામાં તથા જકડવામાં આવે છે. પણ આ ફિક્શ્ચરમાં, કાર્યવસ્તુને પકડવાની સુવિધા સ્પિન્ડલની બાજુમાં જ (ચિત્ર ક્ર. 4) કરી દીધી. કાર્યવસ્તુની કાસ્ટિંગમાં 4 ઉપસેલા ભાગો (પ્રોજેક્શન) હતાં. તેનો ઉપયોગ કાર્યવસ્તુને પકડવા માટે કરવામાં આવ્યો. હાઈડ્રોલિક ક્લૅમ્પિંગની મદદથી એ રેસ્ટિંગ ભાગ પર કાર્યવસ્તુ જકડવામાં આવી. રેસ્ટિંગનો ભાગ સખત હોવાને કારણે કાર્યવસ્તુનો આકાર બદલાયા વિના પણ જકડવાનું દબાણ વધારી શકાયું. યંત્રણની ગતિ વધારીને કામ કરવાની દ્રષ્ટીએ અંતર્ગોળ હિસ્સાની નીચે 3 જગ્યાએ હાઈડ્રોલિક વર્ક સપોર્ટ આપવામાં આવ્યા. આમ કાર્યવસ્તુનો આકાર બદલ્યા વિના, તેને મજબૂતાઈથી પકડવામાં આવી અને યંત્રણની ગતિ વધારીને આવર્તન કાળ (સાઈકલ ટાઈમ) પણ ઘટાડવામાં આવ્યો. આ સેટઅપમાં સંપૂર્ણ યંત્રણ 8 મિનિટમાં પૂરૂં થઇ ગયું.
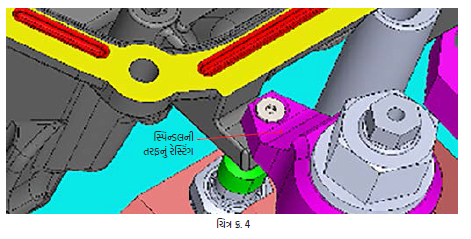
ક. આયોજન અનુસાર, બીજા સેટઅપમાં એ જ ફિક્શ્ચરની બીજી બાજૂનો ઉપયોગ કરવાનો હતો. પ્રથમ સેટઅપની વિશેષતાને કારણે બીજો સેટઅપ તૈયાર કરવાનું પ્રમાણમાં ઘણું સરળ અને સહેલું હતું. પ્રથમ સેટઅપમાં મિલિંગ કરેલ સપાટી પર કાર્યવસ્તુ બેસાડી તથા સંદર્ભ છિદ્રોમાં કાર્યવસ્તુને બેસાડીને પકડવામાં આવી. આમ આ સંપૂર્ણ કાર્યવસ્તુ યંત્રણ માટે ઉપલબ્ધ થઇ શકી. બીજા સેટઅપનું યંત્રણ 5 મિનિટમાં પૂર્ણ કરવામાં આવ્યું હતું.
આ રીતે એક જ ફિક્શ્ચર પર બન્ને સેટઅપ લગાડી એચ.એમ.સી.ની એક જ પૅલેટ પર ગ્રાહકને અપેક્ષિત સુસંગત ગુણવત્તામાં માત્ર 13 મિનિટમાં એક કાર્યવસ્તુનું યંત્રણ પૂરૂં કરવામાં આવ્યું. તમામ પરીક્ષણ કરીને અમે આ ફિક્શ્ચર ગ્રાહકને સુપરત કર્યું. આમાં અમારી ટીમનું અત્યંત મહત્ત્વપૂર્ણ યોગદાન છે. તે સાચું છે કે અમે આ ધંધો નફાકારક રીતે કર્યો છે, પરંતુ તે જ સમયે અમે ગ્રાહકોની નજરમાં ‘વિશ્વસનીય અને સૌથી વધુ પસંદ કરાયેલ સપ્લાયર’ પણ બની ગયા છે.