ઉત્પાદન ક્ષેત્રમાં ગુણવત્તા નિયંત્રણ વિભાગ પર અતિશય ઓછા સમયમાં મોટા અને જટિલ કામોની તપાસ કરીને, એ કામની ગુણવત્તા પ્રમાણિત કરવાની જવાબદારી હોય છે. જો નિર્માણ થનારી દરેક વસ્તુ ચોકસાઈપૂર્વકની અને અચૂક છે કે નહિ, એ નક્કી કરવા માટે તેને ગુણવત્તા પરીક્ષણમાંથી પસાર થવું પડે એમ હોય, તો ઉત્પાદન વિભાગની ક્ષમતા ગુણવત્તા નિયંત્રણ વિભાગની કામગીરી પર નિર્ભર હોય છે. આ કારણે ગુણવત્તા નિયંત્રણ વિભાગ પર કામનો બોજો વધી જાય છે. જો એક જ કાર્યવસ્તુમાં ચકાસવાની બાબતો વધુ હોય. ઉદાહરણ તરીકેઃ - ધાર, વળાંકવાળા ભાગો, ડ્રિલ કરેલ છિદ્રો, ગ્રૂવ્સ, વગેરે, તો આ કાર્ય હજી વધુ મુશ્કેલ બને છે અને પ્રશિક્ષિત અને કુશળ કર્મચારીઓની મોટા પ્રમાણમાં જરૂર પડે છે. ઉત્પાદનના પ્રમાણમાં માગણી અનુસાર હંમેશા ચઢાવ-ઉતાર થતા જ રહેતા હોય છે, એટલે ગુણવત્તા પરીક્ષણ કરનારા કર્મચારીઓની કામગીરી પર તેનો પ્રભાવ પડતો હોય છે. તેથી કેટલાક સમય તેમના કામની ગુણવત્તા સાથે ચેડા થઈ શકે છે.
ગુણવત્તા નિયંત્રણ માટે ઉદ્યોગ ક્ષેત્રમાં વિવિધ તંત્રો/સાધનોનો ઉપયોગ કરવામાં આવે છે. જો કે, દરેક ઇન્સ્ટ્રુમેન્ટની ક્ષમતા અનુસાર તેના ટૉલરન્સ અને ફિટ માપવાની ચોકસાઈમાં અમુક દશાંશ પોઇન્ટમાં મર્યાદા પણ હોય છે. એટલે એ કારણે પણ યંત્રભાગ ઍસેમ્બ્લી સુધી પહોંચે ત્યારે નકારવામાં આવે તેની શક્યતા વધી જાય છે. આવા અસ્વીકાર્ય યંત્રભાગ ઉત્પાદન વિભાગમાં રિપેરિંગ/પુન: પ્રક્રિયા માટે ફરી મોકલવામાં આવે છે અને ઉત્પાદન/યંત્રણ થયા બાદ નાની-મોટી ખામીયો દૂર કરવા એક કુશળ કર્મચારીની નિમણુંક કરવી પડે છે. એનાથી યંત્રણ માટે લાગતો સમય અને ખર્ચ બન્ને વધે છે. ચોકસાઈપૂર્વકના યંત્રણને લીધે આ સમસ્યાનું નિવારણ થઈ શકે છે, પરંતુ એ દરમિયાન માનવીય ક્ષતિ/ભૂલ પ્રત્યે આંખ આડા કાન કરીને ચાલશે નહિ. ઉત્પાદન કાર્યમાં સંપૂર્ણ સ્વચાલન (ઑટોમેશન) સક્ષમ કરવા માટે પ્રથમ દરની ગુણવત્તા ખાતરી હોવી જરૂરી છે.
ગુણવત્તા નિયંત્રણ અને તપાસણી પ્રણાલીની જરૂરિયાત ધરાવતા એક એન્જિનિયરિંગ જૂથે કહ્યું કે, ‘અમને સેંકડો વસ્તુઓના ગુણવત્તા નિયંત્રણ માટે એક તાત્કાલિક પ્રતિસાદ અને માઈક્રોમીટર સ્તરની ચોકસાઈ વાળી સિસ્ટમની જરૂર છે.’
એમની માગણીનો ઊંડાણપૂર્વક અભ્યાસ કરીને અમે એક સરળ ઉપાય શોધી કાઢ્યો. અમે એમને એમના ગુણવત્તા નિયંત્રણ વિભાગમાં લેઝર સ્કૅનિંગ કરનાર એક નાનું મશીન બેસાડવાની ભલામણ કરી.
લેઝર પ્રણાલી કેવી રીતે કામ કરે છે?
લેઝર વિસ્થાપન (ડિસપ્લેસમેન્ટ) સેન્સર પદ્ધતિ પર આધારિત લેઝર માપન તંત્ર, એ આ સિસ્ટમનો મુખ્ય ભાગ છે. જે સ્થાને પારંપરિક પદ્ધતિથી અંતર અથવા ડાયમેન્શન, વગેરેનું માપન કરવું અત્યંત મુશ્કેલ હોય, તેવી જટિલ સપાટી માટે લેઝર પર આધારિત માપન તંત્ર, આ એક વિશેષ પદ્ધતિ વિકસિત કરવામાં આવી છે. આ પ્રણાલીના બીજા તબક્કે ભાગોની અપેક્ષિત જાડાઈ તપાસવા જેવા કામો માટે તેમાં જરૂરી સુધારણા કરેલ છે.
આ લેઝર પર આધારિત એક અતિશય સુવિધાજનક સ્કૅનિંગ મશીન છે. આમાં વૉલ્યુમ ઇલ્યુમિનેશન અને ફોટો ડાયોડ રિસીવર તેમજ, હાઈ રેઝોલ્યુશન કૅમેરા (ચિત્ર ક્ર. 1 અ અને 2 અ) પણ છે. કોઈપણ પ્રતિનિધિક પ્રણાલીમાં નીચે વર્ણવ્યા અનુસાર ઘટકો હોય છે. ઑપ્ટિકલ લેઝર સ્કૅનર, એક ડિટેકશન યુનિટ, એક ડેટા પ્રોસેસિંગ યુનિટ. રિસીવરની આગળ (ચિત્ર ક્ર. 2 બ) ફિલ્ટર્સ અને લેન્સ બેસાડવામાં આવે છે. આ લેન્સ વાઈડ ઍન્ગલ ઍડજેસ્ટમેન્ટ કરીને વસ્તુપર ફોકસ કરવા માટે બેસાડવામાં આવેલ હોય છે. પ્રકાશની જે તરંગલંબાઇ વડે વિક્ષેપ પેદા થઇ શકે છે, તેને ફિલ્ટર દ્વારા અવરોધવામાં આવે છે. લેઝરની તરંગલંબાઇ અનુસાર ફિલ્ટરની પસંદગી કરવામાં આવે છે. અંતરના માપન માટે (ચિત્ર ક્ર. 1 અ) જરૂરિયાત પ્રમાણે સાદું લેઝર બિંદુ અથવા લેઝર કિરણ પર્યાપ્ત હોય છે. લેઝર સ્કૅનિંગ પ્રણાલીમાં જે સપાટીની તપાસણી/નિરીક્ષણ કરવાનું હોય, તેને લેઝર પ્રકાશના બીમ દ્વારા પ્રત્યેક બિંદુ પર સ્કૅન કરવામાં આવે છે. તે કારણે સપાટી પર એક તેજસ્વી બિંદુ નિર્માણ થાય છે. જ્યારે ફોકસ કરવામાં આવેલ લેઝર બીમ કોઈ એક સપાટી પર પડે, ત્યારે ઉત્સર્જીત થતાં કિરણોનું પ્રસરાવું (રેડિએશનનું સ્કૅટરિંગ) એ સપાટીના સ્વરૂપ અને તેની રચના પર નિર્ભર હોય છે. કોઈપણ વસ્તુના સંપૂર્ણ સપાટીની તપાસ કરવી હોય, તો કોઈપણ જગ્યા બાકાત ન રહી જાય એ રીતે, છબી સ્પષ્ટ આવે તે રીતે, લેન્સની રચના કરીને (ફોકસ) લેઝર કિરણો વડે સપાટી પરના પ્રત્યેક બિંદુની તપાસ કરવી જરૂરી હોય છે. પ્રકાશ પકડનાર (લાઈટ રિસીવિંગ) યુનિટ ઇમેજિંગ લેન્સમાંથી ઉપર વર્ણવેલ તેજસ્વી બિંદુનું અવકાશીય સ્થાન એક પીસીડી અથવા સીસીડી જેવા પ્રકાશબિંદુ પોઝિશન ડિટેકટર દ્વારા નોંધે છે. માપન પ્રણાલીમાં સિગ્નલ પ્રોસેસિંગ યુનિટ, પ્રોબની જેમ કામ કરીને વસ્તુના વિસ્થાપનમાં થયેલ બદલાવની ગણતરી કરે છે અને માપનના સમયે સપાટી પર ફરનાર તેજસ્વી બિંદુનું બદલાતું સ્થાન સતત નોંધવામાં આવે છે.
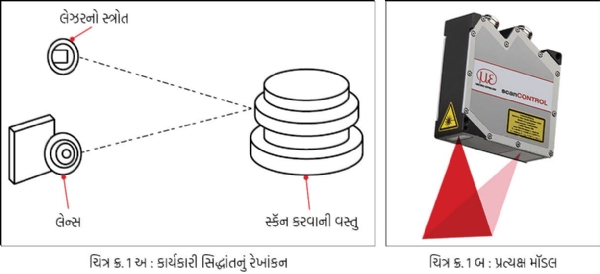
પ્રણાલી દ્વારા વસ્તુના આદર્શ નમુનાનું (માસ્ટર) ત્રણ પરિમાણોમાં સ્કૅનિંગ કરવામાં આવે છે અને સંદર્ભ માટે એ નમુનાનો એક નકશો તૈયાર કરવામાં આવે છે. સ્કૅનિંગ પ્રક્રિયા શરુ કર્યા પૂર્વે એક આરંભિક બિંદુ નિશ્ચિત કરવામાં આવે છે. આ માસ્ટરની સપાટીના લેઝર પ્રતિબિંબ, દરેક સ્કૅનિંગ વખતે સિસ્ટમની સ્મૃતિમાં સંગ્રહિત થઈ જાય છે. સપાટીનું ચયન અનુક્રમે કરી શકાય છે અને તે અનુસાર એ મશીનમાં સ્કૅનિંગ કરી શકાય છે. સંપૂર્ણ નમુનાની સ્કૅનિંગ પ્રક્રિયા પૂરી થયા બાદ સૉલિડ મૉડેલિંગ નિર્મિતિના સૉફ્ટવેઅર દ્વારા એની પુનર્રચના કરવામાં આવે છે. તમારા જોવા માટે આ સૉફ્ટવેઅર એક પ્રી-વ્યૂ તૈયાર કરી શકે છે. ગુણવત્તા નિશ્ચિત કરનાર વિભાગના કર્મચારીઓ આ તબક્કે પોતાનું યોગદાન આપી પરિમાણમાં હજી વધુ સુધારા કરી શકે છે. જે ક્ષેત્રનું વિશ્લેષણ કરવાનું હોય છે, તે ગમે એટલું મોટું હોઈ શકે છે અને સ્થાનસંબંધી સૂક્ષ્મતા માઈક્રોમીટર કરતા પણ નાની હોઈ શકે છે. લેઝર બિંદુનું સપાટી પરનું સ્થાન કોઈપણ તબક્કે અત્યંત ચોકસાઈપૂર્વક નિશ્ચિત કરી શકાય છે, એટલે એ શક્ય બને છે.
ઉપયોગ કરવાની રીત
વિશ્વસનીયતાની નવી માંગને પહોંચી વળવા માટે જાણીતી ગણિતિક પદ્ધતિઓ અને તકનીકોનું (ઇન્ટરફેરોમેટ્રિક, સ્કૅટરિંગ, ટ્રઁગ્યુલેશન, ફ્રિન્જ પ્રોજેક્શન વગેરે) હવે નવેસરથી અધ્યયન કરી અને એમનો વિકાસ કરવામાં આવ્યો છે. ખાસ કરીને ટ્રઁગ્યુલેશન પર આધારિત પદ્ધતિનો ઉપયોગ રેંજ સેન્સિંગ, અથવા 3D આકાર પરીક્ષા, ટોપોગ્રાફિક મૂલ્યાંકન અને ખરબચડી સપાટીના સૂક્ષ્મ પરીક્ષણ, વગેરે કામોમાં મોટા પ્રમાણમાં કરવામાં આવે છે. પ્રત્યેક સ્કૅનિંગ વખતે તપાસવામાં આવતી સપાટીની તુલના, સેન્સર તેની સ્મૃતિમાં રહેલ કાલ્પનિક સંદર્ભ સપાટીની સાથે કરે છે અને પછી આ બંને સપાટીઓ વચ્ચેના સાપેક્ષ વિસ્થાપનનું અંતર માપીને રેકોર્ડ કરે છે. આ નકશો તેની સ્મૃતિમાં સંગ્રહિત કરવામાં આવે છે. તેનો ઉપયોગ ઉત્પાદન વિભાગમાં સક્રિય મશીનો પર જરૂરિયાત પ્રમાણે કરવામાં આવે છે. સ્કૅનિંગ કરતી વખતે વસ્તુ ત્રણેય અક્ષમાં, 360 અંશમાં ફેરવવામાં આવે છે. જો ગોળ ફેરવવું શક્ય ન હોય તો, સ્વચાલન પરનો વર્ક લોડ ઓછો કરવા માટે સ્કૅનિંગ યુનિટની એક ઍરે આયોજિત કરવી શકય બને છે. (ચિત્ર ક્ર. 3 અ અને બ)
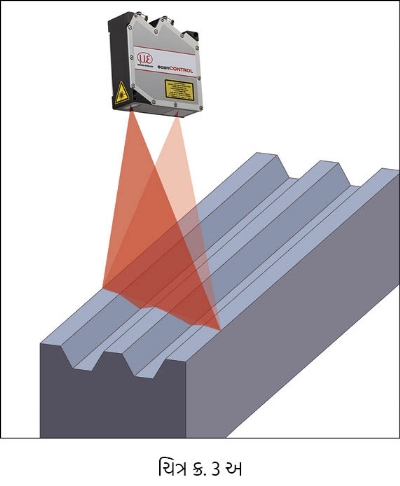
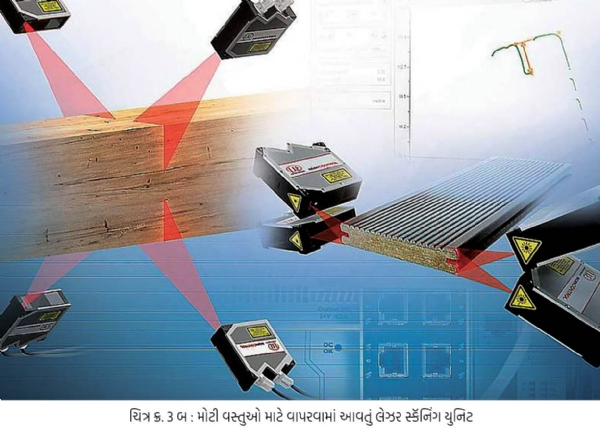
એક જ વસ્તુ માટે આ તપાસણી વપરાશકર્તાની જરૂરિયાતો મુજબ જોઈએ તેટલી વાર કરી શકાય છે. અગાઉ ઉલ્લેખ કરવામાં આવ્યા પ્રમાણે ચિત્ર ક્ર. 3 અ અને બ માં દર્શાવ્યા પ્રમાણે સ્કૅનિંગ પ્રણાલીની ઍરે આયોજિત કરવી શક્ય હોય છે. સ્કૅનિંગ યુનિટની સંખ્યાપર આધારિત વસ્તુના ભાગ અથવા સેક્શન અલગ પાડવામાં આવે છે. જ્યાં સુધી તેને કારણે કોઈ જાતનો વિક્ષેપ સર્જાતો નથી, ત્યાં સુધી જો બન્ને વિભાગો એકબીજા પર ઓવરલૅપ થાય, તો પણ ચિતાનું કોઈ કારણ ઉદ્દભવતું નથી. પણ જો એ કારણે કોઈ વિક્ષેપ સર્જાય, તો અલગ અલગ તરંગલંબાઈના લેઝર વાપરી શકાય છે. (ચિત્ર ક્ર. 4 અ, 4 બ) જો 2 અથવા 3 સ્કૅનિંગ યુનિટ કાર્યરત હોય, તો એ કાર્ય અત્યંત સરળ થઈ જાય છે. પરંતુ જો 3 થી વધુ સ્કૅનિંગ યુનિટ વપરાશમાં હોય, તો અલગ અલગ ક્ષેત્ર નિયત કરવા પડે છે અને સ્કૅનિંગ મશીન તે પ્રમાણે આયોજિત કરવા પડે છે. કેમકે ઉપલબ્ધ લેઝર તરંગલંબાઈની સંખ્યા મર્યાદિત હોય છે.
પરિણામો ઑનલાઇન મોડમાં વપરાશકર્તા સમક્ષ રજૂ થાય છે અને ઉત્પાદનમાંના અસંગત ઉત્પાદનોને ઝડપથી અલગ કરી શકાય છે. (ચિત્ર ક્ર. 5) ઉત્પાદન યંત્રણા જે ગતિથી કામ કરી શકે છે, તેટલી જ ગતિથી આ પ્રણાલી કામ કરી શકે છે. સ્કૅનિંગનો દર પ્રતિ વસ્તુ ઓછામાં ઓછો 3 સેકંડ જેટલો હોઈ શકે છે. પરંતુ એ તે વસ્તુની જટિલતા અને આકાર પર નિર્ભર હોય છે. સરળ ઉત્પાદન માટે આ દર વધુ પણ હોઈ શકે છે. આ સાથે જોડાયેલ સૉફ્ટવેઅર પૅનલમાં ઉત્પાદનની વિગતો બતાવવામાં આવી છે. સૉફ્ટવેઅર બહુરંગી નકશાના રૂપે આઉટપુટ આપે છે. તેથી ખામીયુક્ત ક્ષેત્રને ઓળખવામાં મદદ મળે છે અને એમાં સરળતાથી સુધારા કરી શકાય છે.
ઉદાહરણ
આપણે સ્પ્રૉકેટ વ્હિલ ટૂથ તપાસનું એક જટિલ ઉદાહરણ જોઈએ. ચિત્ર ક્ર. 6 અ માં દર્શાવ્યા મુજબ લેઝર સ્કૅનિંગ મશીન પર સ્પ્રૉકેટ ટૂથનું સ્કૅનિંગ કરીને ચિત્ર ક્ર. 6 બ અને ચિત્ર ક્ર. 6 ક પ્રમાણે નકશો તૈયાર કરવામાં આવે છે. બે દાંતા વચ્ચેનો કોણ, બે દાંતા વચ્ચેના ખાંચની લંબાઈ, દાંતાની ઊંડાઈ, વક્રતા અથવા પ્રોફાઈલ, પિચ અને સૌથી અગત્યનું, વ્હીલની સપાટીનું ફિનિશ, એ પૅરામીટર તપાસવામાં આવશે. આ ઉપરાંત, સિસ્ટમ વસ્તુ પરના ગોબા, દાંતા વાંકાચૂકા છે કે સમતલ અથવા દાંતાની વ્હીલ પરની અલાઈનમેન્ટ પણ તપાસી શકે છે.
લેઝરનો વિવિધ કામો માટે ઉપયોગ
આ ટેકનોલોજીનો ઉપયોગ કરીને વસ્તુની ગુણવત્તા ચકાસવી અને પ્રમાણિત કરવી, આ બન્ને કાર્ય માટે એક જ વ્યક્તિની જરૂરત પડે છે. કાસ્ટિંગના ઉદ્યોગમાં યંત્રણ પૂર્વે પરિમાણોની મર્યાદા સખત નથી હોતી. એ કારણે પરિમાણોની તપાસ અત્યંત ઝડપથી કરી શકાય છે. અયોગ્ય કાસ્ટિંગને કારણે ઉદ્ભવનારા દોષ/ભૂલ અથવા વાતછિદ્રો (બ્લો હોલ) તદ્દન માઈક્રોમીટરના સ્તરે શોધવું શક્ય હોય છે. એ કારણે જરૂર પડે ત્યારે એનો ઉપયોગ સપાટી પરીક્ષણના સાધન તરીકે પણ કરી શકાય છે. એથી વિપરીત, પ્લાસ્ટિક મોલ્ડિંગ ઉદ્યોગ ક્ષેત્રમાં જ્યારે ડાયના દબાણથી નિર્માણ કરવામાં આવેલ વસ્તુના આંતરિક ભાગમાં દાંતા હોય અથવા મોલ્ડ કરવામાં આવેલ વસ્તુ ટૉલરન્સ સીમાની બહાર હોય, ત્યારે એવા દોષ અત્યંત સરળતાથી ઓળખી શકાય છે, જે સરળ દ્રષ્ટિ આધારિત પરીક્ષણોમાં છૂટી જતી હોય છે. રબર ઉદ્યોગ ક્ષેત્રમાં રિંગ, બુશિંગ જેવા પાછળથી કઠણ કરવામાં આવતી હોય, તેવી વસ્તુમાં સરળ ફિટિંગ માટે ઉચ્ચ સ્તરીય ચોકસાઈ જરૂરી હોય છે. આ સિસ્ટમને કારણે તપાસણી માટે લાગતા સમયમાં પણ બચત થઈ શકે છે.
સમતલ સપાટીના સ્કૅનિંગ માટે આ સિસ્ટમ કોઈપણ ખાડો, કોઈપણ ગોબા અથવા ફૂગી ગયેલ ભાગ, કોણ, સપાટપણું અને વસ્તુના પરિમાણો તપાસી શકે છે.
ચોકસાઈના સ્તરની સાથે સાથે આ પ્રણાલી નાનીથી લઈને મોટામાં મોટી વસ્તુઓ માટે પણ તેટલી જ પરિણામકારક અને ઉપયોગી નીવડે છે, એ એક બીજો ફાયદો છે. ઑટોમેટિવ ઉદ્યોગ ક્ષેત્રમાં નાનામાં નાના સ્ક્રૂ થી ચૅસી જેવી વિશાળ વસ્તુઓ, સાદા બારથી લઈને દરવાજાની જટિલ ડિઝાઈન સુધી, બધું જ સ્કૅન કરીને તપાસવાનું કામ આ પ્રણાલી કરી શકે છે. (ચિત્ર ક્ર. 8) તે માટે તેને અલગ અલગ ઉત્પાદન વિભાગમાં લઈ જવું શક્ય છે. આ પ્રણાલીના માત્ર એક જ યુનિટનો ઉપયોગ કરીને એક પ્લાન્ટના બધા જ ઉત્પાદનો સહજતાથી તપાસી શકાય છે. દરેક જગ્યાએ આ યુનિટ માત્ર પ્લગ-ઇન કરો અને કામની શરૂઆત કરો, એટલી સરળતાથી ચલાવી શકાય છે. આ પ્રણાલી સંપૂર્ણપણે સુરક્ષિત છે. કેમકે આ પ્રણાલીમાં દ્વિતિય શ્રેણીના લેઝરનો ઉપયોગ કરવામાં આવે છે. આમાં કોઈપણ યાંત્રિક ભાગ નથી, એટલે કોઈપણ પ્રકારની સેફટી સ્વિચ અથવા મશીન સંબંધી વિલંબ થતો હોવાને કારણે પ્રણાલી કાર્યાન્વિત થવામાં સમય લાગે એવું પણ નથી. એમાંથી હાઈ રિઝોલ્યુશન, ઝડપી સ્કૅનિંગ અને ઉચ્ચ કૉન્ટ્રાસ્ટ વાળી સ્પષ્ટ પ્રતિમા મળે છે, એ લેઝર સ્કૅનિંગ પ્રણાલીનો સૌથી મોટો ફાયદો.
પ્રણાલીના ઉપયોગ દરમિયાન લેવાતી કાળજી
આ પ્રણાલી ઉત્પાદન વિભાગે નિર્માણ કરેલ સર્વ ઉત્પાદન નાપાસ કરીને તેમને મોટો આઘાત આપી શકે છે. અહીં, અમુક માનવીય ભૂલને કારણે ખામીયુક્ત વસ્તુ, આદર્શ નમૂના (માસ્ટર) રૂપે પસંદ કરવામાં આવી હોય તો આવી ગરબડ થઈ શકે છે. આને ટાળવા માટે, વપરાશકર્તાઓએ પૂરતી કાળજી લઈને આદર્શ નમૂનો વિકસાવવું જોઈએ. તદ્દન દોષરહિત માસ્ટર બનાવવા માટે વધુ પ્રયત્નો કરવાથી આપમેળે જ ગુણવત્તા નિયંત્રણ યુનિટની તકલીફો અને સમય બન્નેની બચત થશે. આ પ્રણાલી કોઈપણ વાતાવરણમાં કામ કરી શકે છે. કોઈપણ જગ્યાએથી આવતા અથવા આજૂબાજૂના પ્રકાશને કારણે અંતિમ પરિણામમાં કોઈ વધારાની ભૂલ ઉમેરાતી નથી. એનો અર્થ એ કે આ પ્રણાલી સૂર્યપ્રકાશ અથવા તો અંધારાવાળા ઓરડામાં પણ એટલી જ ચોકસાઈથી કામ કરે છે. તાપમાનમાં થતા ફેરફારનો માપનના પરિણામ પર કોઈ પ્રભાવ પડતો નથી, પરંતુ એને જે વસ્તુ તપાસવી હોય, તેનું તાપમાન અપવાદરૂપ હોઈ શકે છે. (કારણ વસ્તુના પોતાના તાપમાન પ્રમાણે તેના પરિમાણોમાં બદલાવ થતો હોય છે.)જાડાઈ અને વોલ્યુમ ઉપરાંત, આ પ્રણાલી કદ, સપાટપણું, લંબાઈ, વિકૃતિ (ડિસ્ટૉર્શન), તરંગમયતા (વેવ્હીનેસ), સમ પ્રતલતા (કૉ- પ્લેનેરિટી) વગેરે પરિમાણો માટે પણ સારી રીતે ચાલે છે. એનો દેખભાળનો ખર્ચ અત્યંત ઓછો છે.
પહેલાં તાપમાનમાં તફાવત, છબીઓની પ્રક્રિયામાં ભૂલો અને ગાણિતિક મૉડેલિંગની મર્યાદાઓને કારણે માપમાં થતી ભૂલો એવી મર્યાદાઓ હતી, જે હવે લગભગ નહીવત છે. હવે સપાટી પર રહેલ કચરાને કારણે અથવા બાહ્ય તત્વોને (ફૉરેન બૉડીઝ) કારણે મોટાભાગની ભૂલો સર્જાતી હોય છે.
આ પ્રણાલીની કિંમત, એ કયા કામ માટે ઉપયોગમાં લેવાની છે, એના ઉપયોગ દ્વારા કેટલી ચોકસાઈ અપેક્ષિત છે, વગેરે બાબતો પર આધારિત હોય છે. એક ઉચ્ચ રેઝોલ્યુશન વાળી અત્યંત સાદી 1D સ્કૅનિંગ પ્રણાલી, ઓછા રેઝોલ્યુશન વાળી 3D પ્રણાલી કરતા વધુ મોંઘી હોઈ શકે છે.
સુધારેલા ગુણવત્તા પરીક્ષણ દરને કારણે ઉત્પાદન વિભાગની તાણ ઓછી થઈ શકે છે અને જે ગુણવત્તા નિયંત્રણ પ્રક્રિયામાં તાણની પ્રશંસા કરે છે, તેમના ચહેરાઓ પર આપણે સ્મિત જોઈ શકીએ છીએ.