સિલેક્ટિવ લેઝર મેલ્ટિંગ અને લેઝર ડિપોઝિશન વેલ્ડિંગ એ ઍડિટિવ મૅન્યુફૅક્ચરિંગના બે પ્રકાર છે. આ બન્નેના મૂળ સિદ્ધાંતો, વાસ્તવિક તકનીક અને ઉપયોગો વિશે વિગતવાર માહિતી આપીને પરંપરાગત સબટ્રૅક્ટિવ મૅન્યુફૅક્ચરિંગ સાથે તેને જોડવાની તકનીકનું વર્ણન કરતો એક માહિતીપૂર્ણ લેખ.
ડી.એમ.જી. મોરી કંપનીએ હાલમાં જ ભારતીય માર્કેટમાં ઍડિટિવ મૅન્યુફૅકચરિંગના બે ઉત્પાદ (પ્રૉડક્ટ) રજૂ કર્યા છે. ડી.એમ.જી મોરી એ પ્રથમ કંપની છે જેણે ઍડિટિવ અને સબટ્રૅક્ટિવ બંને પ્રણાલીઓને એક જ મશીનમાં ઉતારેલ છે. 3D પ્રિન્ટિંગ પછી કાર્યવસ્તુનું ફિનિશ, કાસ્ટિંગ કરેલી કાર્યવસ્તુ જેવું દેખાતું હોય છે. એટલા માટે એના પર યંત્રણ કરવું જરૂરી હોય છે. અમારા મશીન પર એ જ સેટઅપમાં આગળનું યંત્રણ પણ કરી શકાય છે.
એક જ સેટઅપમાં પ્રિન્ટિંગ તથા યંત્રણ
આ લેખમાં આપણે ઍડિટિવ ઉત્પાદન ટેકનિક વિશે જાણકારી મેળવીશું. એમાં મુખ્યત્વે બે ટેકનિક હોય છે.
1. સિલેક્ટિવ લેઝર મેલ્ટિંગ (SLM) જેને પાવડર બેડ ટેકનિક પણ કહેવામાં
આવે છે.
2. લેઝર ડિપૉઝિશન વેલ્ડિંગ જેને પાવડર નૉઝલ ટેકનિક પણ કહેવામાં આવે છે.
હવે આ બન્ને પદ્ધતિ વિશે જાણીએ:
સિલેક્ટિવ લેઝર મેલ્ટિંગ (SLM) / પાવડર બેડ ટેકનિક
સિલેક્ટિવ લેઝર મેલ્ટિંગ (SLM) પદ્ધતિમાં એક ક્લોઝડ પ્રોસેસ ચેમ્બર (ચિત્ર ક્ર. 2) હોય છે, જેમાં આર્ગૉન ગૅસ ભરેલ હોય છે. આ દબાણયુક્ત ચેમ્બરમાં 3D પ્રિન્ટિંગ કરવામાં આવે છે. લેઝરની મદદથી કોઈ પણ બે મટીરિયલ ઓગાળીને ફ્યુઝ કરવામાં આવે છે, ત્યારે ઉષ્ણતા અને હવામાં રહેલ ઑક્સિજનને લીધે ઑક્સિડેશન થવાની શકયતાઓ વધી જાય છે. એ ટાળવા માટે બે અલગ અલગ ગૅસનો ઉપયોગ કરવામાં આવે છે, આર્ગૉન અને નાઈટ્રોજન. પરંતુ નાઈટ્રોજન દરેક ધાતુ માટે યોગ્ય નથી હોતો. જેમ કે ઍલ્યુમિનિયમ, ટાઈટેનિયમ અથવા તાંબા જેવી હાઈ રિઍક્ટિવ ધાતુઓ માટે નાઈટ્રોજન વધુ પ્રભાવશાળી સાબિત નથી થતો. એટલા માટે એ ધાતુઓ માટે આર્ગૉન ગૅસનો ઉપયોગ કરવામાં આવે છે. કેમકે આર્ગૉન ગૅસ દરેક ધાતુઓ પર સારી રીતે આવરણ તૈયાર કરી શકે છે એટલે ઑક્સિડેશન નથી થતું.
વસ્તુ નિર્માણ ગતિ (બિલ્ડ રેટ)
આ પદ્ધતિ પ્રમાણે વસ્તુ નિર્માણ ગતિ 84 ગ્રામ્સ પ્રતિ કલાક હોય છે, જે એક સાધારણ દર છે. જલ્દી પ્રતિક્રિયા દેનાર ટાઇટેનિયમનું ગલનબિંદુ (મેલ્ટિંગ પોઈન્ટ) વધુ હોવાને લીધે એના ફ્યુઝનમાં પણ વધુ સમય લાગે છે. સ્ટીલની કાર્યવસ્તુઓ માટે 10 સેમી3 પ્રતિ કલાકની ગતિ નોંધાતી હોય છે, કેમ કે સ્ટીલનું ગલનબિંદુ એનાથી ઓછું હોય છે. સ્ટીલમાં આપણે 110 થી 120 ગ્રામ પ્રતિ કલાકની ગતિ મેળવી શકીએ છીએ.
ઉદાહરણ રૂપે ચિત્ર ક્ર. 3 માં દર્શાવેલ અત્યંત જટિલ ભૂમિતિ અને આકારની નાની વસ્તુ જ્યારે બનાવવાની હોય, ત્યારે પાવડર બેડ ટેકનિકનો ઉપયોગ કરવામાં આવે છે. આ પાવડર બેડ પદ્ધતિમાં વસ્તુ માટે એક બિલ્ડિંગ પ્લેટફોર્મ હોય છે. સાથે જ રીકોટર પ્રણાલી પણ હોય છે. જે ધાતુના ઉપયોગથી પ્રિન્ટિંગ કરવાનું હોય, તે ધાતુનો પાવડર એક કાર્ટ્રિજમાં ભરેલો હોય છે. દરેક કોટની જાડાઈ અગાઉથી જ નિર્ધારિત કરવામાં આવેલ હોય છે, જે 20 થી 100 માઈક્રોનની વચ્ચે હોય છે.
રીકોટર દરેક વખતે એ માત્રામાં પાવડર લઈને એટલી જ જાડાઈનું કોટિંગ બનાવે છે. ત્યાર બાદ એ કોટિંગ પરથી લેઝર બીમ પસાર કરવામાં આવે છે અને નિર્ધારિત મૉડલ અનુસારના પરિમાણો (માપ) મુજબ એટલા જ નિર્ધારિત હિસ્સામાં કાર્ય કરી ત્યાંના પાવડરને ઓગાળી દે છે. એટલા માટે જ એને સિલેક્ટિવ લેઝર મેલ્ટિંગ કહેવામાં આવે છે કેમ કે અન્ય સ્થાનો પર ચડાવેલ કોટિંગ જેમ છે તેમ જ રહે છે. આમ પ્રથમ પડ બન્યા પછી ફરી પાવડરનું એક વધુ કોટિંગ કરવામાં આવે છે. એ કોટમાંથી પણ પૂર્વ-નિર્ધારિત જગ્યાઓમાંથી ફરી પાવડર ઓગળાવીને બીજા કોટિંગને અંતિમ સ્વરૂપ આપવામાં આવે છે. આમ કોટિંગ વધારતા જઈ વસ્તુ બનાવવામાં આવે છે. કોટિંગની જાડાઈ ધાતુની વિશિષ્ટતાઓ પર આધારિત હોય છે.
ધારો કે આપણે 10 મિમી. ઉંચી વસ્તુ બનાવી છે. એમાં દરેક કોટિંગની ઊંચાઈ 20 માઈક્રોન છે. એવામાં પાવડરના સ્તરની ઊંચાઈ, અત્યાર સુધી બનેલા કાર્યવસ્તુની ઊંચાઈ જેટલી જ હોવી જોઈએ. હવે પછીનો સ્તર બનાવવા પૂર્વે પ્લેટફોર્મને નીચેની તરફ હલાવી, ઈચ્છિત ઊંચાઈ સુધી લાવવામાં આવે છે. જ્યારે કાર્યવસ્તુ પૂર્ણ રૂપે તૈયાર થઇ જાય ત્યારે એ પાવડરમાં પૂર્ણ રીતે ડૂબેલી હોય છે. કામ પૂર્ણ થયા બાદ બિલ્ડ પ્લેટફોર્મ ફરીથી ઉપર ઉઠાવવામાં આવે છે અને કાર્યક્ષેત્રમાંથી વધારાનો પાવડર દૂર કરવામાં આવે છે.
આ પ્રકારનું મશીન (ચિત્ર ક્ર. 4) નીચે લખેલ બંને પરિમાણોની કાર્યવસ્તુઓ બનાવવા માટે ઉપલબ્ધ છે.
• 300 X 300 X 300 (મિમી)
• 125 X 125 X 200 (મિમી)
આ બહારી માપોની અંદર બેસતી કોઈ પણ આકારની કાર્યવસ્તુઓ ગમે તેટલી સંખ્યામાં એક સાથે બનાવી શકાય છે. કાર્યવસ્તુઓ ગમે તેટલી અલગ અલગ હોય તો પણ નિર્માણની પૂર્વ નિર્ધારિત ગતિથી ધાતુ ઓગાળીને 3D પ્રિન્ટિંગ કરી શકાય છે.
ઉપયોગમાં લેવાતા ધાતુ
આ ધાતુ અગાઉ 123 માઈક્રોન અને 63 માઈક્રોન જેટલા સૂક્ષ્મ કણના પાવડરના રૂપે મળે છે. આનાથી પણ સૂક્ષ્મ પાવડર બજારમાં ઉપલબ્ધ છે પણ એ ખૂબ મોંઘી હોય છે. પાવડરના નિર્માતાઓ ગ્રાહકોની ઈચ્છા મુજબ પાવડરનું મિશ્રણ બનાવી દેતા હોય છે. આ પાવડર સંપૂર્ણ શુદ્ધ હોય છે.
એનો ઉપયોગ અગાઉ ઓછી સંખ્યામાં ઉત્પાદન કરવામાં આવતી જટિલ કાર્યવસ્તુ માટે અત્યંત પ્રભાવશાળી પદ્ધતિથી થઇ શકે છે. જેમ કે, લોકોમોટિવનો એક યંત્રભાગ જો આપણે તરત જ બનાવવો હોય અને એ માટે જો પારંપરિક પદ્ધતિ અપનાવવી હોય, તો એની ડાય તથા પૅટર્ન બનાવવી, કાસ્ટિંગ કરવું, ત્યાર બાદ એનું યંત્રણ કરવું વગેરે અનેક કાર્યો કરવા પડે છે. આ પૂરી પ્રક્રિયામાં એક થી દોઢ મહિનાનો સમય લાગી જતો હોય છે. જો આવી રીતે માત્ર 5 થી 6 પાર્ટ બનાવવાના હોય તો એ ખૂબ મોંઘા પડે છે. જ્યારે એક કે બે દિવસમાં જ આ પાર્ટ તૈયાર કરવા જરૂરી હોય ત્યારે SLM તકનીક જ સૌથી પ્રભાવશાળી સાબિત થાય છે. ધાતુના મિશ્રણનું વિવરણ આપીને પાવડર બનાવી શકાય છે. કાર્યવસ્તુનું આરેખન મશીનના સૉફ્ટવેઅરમાં નાખી, મશીનને યોગ્ય પૅરામીટરમાં સેટ કરીને તરત જ નિર્માણ કરી શકાય છે. હવે આપણે બીજી તકનીક વિષે જાણીએ.
લેઝર ડિપૉઝિશન વેલ્ડિંગ
લેઝર ડિપૉઝિશન વેલ્ડિંગને પાવડર નૉઝલ તકનીક પણ કહેવામાં આવે છે. પારંપારિક પદ્ધતિમાં કોઈ વેલ્ડર જે રીતે વેલ્ડિંગ રોડ ધાતુની સપાટી પર વેલ્ડિંગ ટોર્ચની મદદથી ઓગાળે છે અને પછી મટીરિયલ એક બીજા સાથે વેલ્ડ થઇ જાય છે અર્થાત બિલ્ડ થઇ જાય છે, એજ રીતે આ પ્રક્રિયામાં સપાટી પર ધાતુના પાવડરનો ફુવારો કરવામાં આવે છે અને એક લેઝર બીમની મદદથી એને વેલ્ડ કરવામાં આવે છે. આ પ્રક્રિયા ખુલ્લામાં થાય છે.
ચિત્ર ક્ર. 5 માં લેઝર ડિપૉઝિશન વેલ્ડિંગની રચના દર્શાવામાં આવી છે. ચિત્રમાં લેઝર બીમ લાલ રંગ દ્વારા દર્શાવેલ છે. એની આસપાસ કાળા રંગની તૂટેલી રેખાઓ ધાતુનો પાવડર દર્શાવે છે, તથા વેલ્ડિંગ પ્રક્રિયાને ઢાંકીને સુરક્ષિત રાખનાર ગૅસ બ્લુ રંગની રેખાઓ દ્વારા દર્શાવવામાં આવેલ છે. વધુ વેટેજના લેઝરનો ઉપયોગ કરી પાવડર ઓગાળી એને 3-5 મિમી. વ્યાસનો દ્રવરૂપ ધાતુનો મેલ્ટ પૂલ બનાવવામાં આવે છે. કોઈ પણ જગ્યાએ સમારકામ કરવું, નમુના ઉત્પાદ (પ્રોટોટાઈપ) બનાવવું, લેપન કરવું (કોટિંગ) વગેરે માટે આ પ્રક્રિયા અપનાવવામાં આવે છે.
ચિત્ર ક્ર. 6 માં જે ભાગની મરમ્મત થઇ રહી છે એ એન્જિનના ટાઈ રોડ કેસિંગનો એક ભાગ છે. એનો ઇનલેટ ફ્લઁજ ખરાબ થઇ ગયેલ હતો. પૂર્ણ એન્જિન હાઉસિંગ ફેંકી દેવાને બદલે મૂળ ધાતુના પાવડરના ઉપયોગ દ્વારા તૂટેલ ફ્લઁજનું સમારકામ ત્યાં જ થઇ શક્યું. 3D પ્રિન્ટિંગ દ્વારા, સમારકામ કરેલા યંત્રભાગનું યંત્રણ ત્યાં જ કરી શકાય છે.
વસ્તુ નિર્માણની ગતિ (બિલ્ડ રેટ)
લેઝર ડિપૉઝિશન વેલ્ડિંગની પ્રક્રિયા દ્વારા વસ્તુ નિર્માણની ગતિ સિલેક્ટિવ લેઝર મેલ્ટિંગની તુલનામાં દસ ગણી વધુ છે. સ્ટીલ માટે 750 ગ્રામ પ્રતિ કલાક અથવા 90 સેમી.3 પ્રતિ કલાકની ગતિએ ઉત્પાદન કરી શકાય છે. આ પદ્ધતિમાં લગભગ 3મિમી. જાડાઈનું કોટિંગ કરી શકાય છે. આ રીતે આ પ્રક્રિયામાં વધુ ઝડપે વસ્તુઓ બનાવી શક્ય હોય છે, પરંતુ SLM જેટલી જટિલતા જાળવવી સંભવ નથી.
વેલ્ડિંગ ગુણવત્તા
વેલ્ડિંગમાં પોરૉસિટી, ક્રૅકિંગ જેવી ખામીયો સર્જાઈ શકે છે. એ ટાળવા માટે વેલ્ડ મેલ્ટ પૂલના આકારને વારંવાર માપીને લેઝરનું બળ એના અનુકૂળ બનાવવું જરૂરી હોય છે. લેઝર બીમનું નિરીક્ષણ રાખનાર ઑનલાઈન કૅમેરાના માધ્યમથી તાપમાનનું માપ લઈને આ ફીડબૅક આપવામાં આવે છે. મોલ્ડ તથા વાલ્વ નિર્માતા આ મશીનના બે પ્રધાન ગ્રાહક છે કેમ કે આ ક્ષેત્રોમાં ટૂલ તથા પાર્ટનું મૂલ્ય વધુ હોય છે, પરંતુ ઉત્પાદન ઓછી સંખ્યામાં કરાય છે.
મશીનનો આકાર
DMU 65 મોનોબ્લૉક મશીનનો આકાર (ચિત્ર ક્ર. 7) કાર્યક્ષેત્રમાં Ø 500 X 400મિમી. હોય છે. એક જ સમયે 500 મિમી. વ્યાસ તથા 400 મિમી. ઊંચાઈ વાળો પાર્ટ અત્યંત ઝડપથી બનાવી શકાય છે. સાથે સાથે વર્તમાન પાર્ટ પર અને મટીરિયલ કોટિંગનું કામ પણ આ આકારની અંદરની અંદર કરી શકાય છે. પાવડર બેડ તકનીક દ્વારા અનેક જટિલ વસ્તુઓ બનાવી શકાય છે. કેમ કે એમાં આ કોટિંગની જાડાઈ 20 માઈક્રોનથી શરુ થાય છે. એ ઉપરાંત મશીનના કાર્યક્ષેત્રમાં જે સમાવિષ્ટ થઇ શકે તે અલગ અલગ પ્રકારના પાર્ટ બનાવવાનું પણ સંભવ છે. આ પ્રક્રિયા દ્વારા બનેલી કાર્યવસ્તુઓનું (ચિત્ર ક્ર. 8) ફિનિશિંગ કરવા એ જ મશીનના સ્પિન્ડલ પરના લેસર હેડને કાઢી શકાય છે અને એને સ્થાને યંત્રણ કરનાર સ્પિન્ડલમાં કટિંગ ટૂલ બેસાડી એજ જગ્યાએ યંત્રણ પણ કરી શકાય છે. મોટા આકારની કાર્યવસ્તુઓ માટે મશીનની આ વિશેષતા વધુ ઉપયોગી સાબિત થાય છે.
પાવડર નૉઝલ માટે ઉપયોગમાં
લેવાતા ધાતુ
પાવડર બેડ વિધિમાં ઉપયોગમાં આવનાર પાવડરના કણોના આકારની તુલનામાં આ પ્રક્રિયામાં 50 થી 200 માઈક્રોન સુધીના આકારના કણોનો પાવડર ઉપયોગમાં લઇ શકાય છે.
ડી.એમ.જી. મોરીનું મશીન આ વિભિન્ન સંયોજનોમાં ઉપલબ્ધ છે
1. સ્ટૅન્ડ અલોન પાવડર નૉઝલ
2. પાવડર નૉઝલ તથા 5 અક્ષોમાં સંભવ મિલિંગના સંયોજન વાળું હાઈબ્રીડ
3. પાવડર નૉઝલ તથા ટર્નિંગના સંયોજન વાળું હાઈબ્રીડ
પ્રોસેસ શૃંખલા (પ્રોસેસ ચેઈન)
ચિત્ર ક્ર. 10 માં ચાર અલગ અલગ પ્રક્રિયા શ્રેણી દર્શાવવામાં આવી છે. પ્રક્રિયા શ્રેણી એટલે એક પાર્ટ બનાવવા માટે જરૂરી તથા એકબીજા પર નિર્ભર રહેનાર પ્રક્રિયાની શ્રેણી.
• પ્રથમ પ્રક્રિયા છે કમ્પ્યુટર મૉડેલિંગ. આમાં કાર્યવસ્તુનું 3D મૉડેલ બનાવવાનું અને એના આઉટપુટ STEP અથવા STL ફોરમૅટમાં બનાવવાનું કામ થાય છે.
• ત્યાર બાદ પાવડર નૉઝલ મશીનમાં CAM પ્રણાલીની મદદથી અથવા પાવડર બેડ મશીન માટે સ્લાઈસરમાં પ્રોગ્રામિંગ કરવું જરૂરી હોય છે. જે મશીન પર કાર્યવસ્તુનું નિર્માણ કરવું હોય તે મશીન માટે વિશેષ પોસ્ટ પ્રોસેસર દ્વારા પ્રોગ્રામિંગ પ્રક્રિયા કરવામાં આવે છે.
• એના પછી મશીન પર 3D પ્રિન્ટિંગની પ્રક્રિયા કરવામાં આવે છે. પાવડર બેડ મશીનના સંદર્ભે કમ્પ્યુટર પર બનાવવામાં આવેલ મૉડલ મુજબ ધાતુને ઓગાળી કાર્યવસ્તુ બનાવવામાં આવે છે.
• ધાતુની સાથે થનારી તમામ ઍડિટીવ ઉત્પાદન કાર્યપ્રણાલી અનુસાર ચોથી પ્રક્રિયામાં બનેલ કાર્યવસ્તુનું જરૂરીયાત પ્રમાણે મશીનિંગ કરીને એને અંતિમ સ્વરૂપ આપવામાં આવે છે. અટપટી ભૂમિતિ વાળી કાર્યવસ્તુઓના યંત્રણ માટે સામાન્ય રીતે 5 અક્ષીય મશીનનો ઉપયોગ થાય છે.
ક્યારેક પહેલા યંત્રણ અને પછી પ્રિન્ટિંગ કરવામાં આવતું હોય છે. આ પદ્ધતિથી કાર્યવસ્તુ મશીનિંગ સેન્ટરમાં જ પૂર્ણ રૂપે બનાવવામાં આવે છે. પરંતુ જટિલ હિસ્સો બિલ્ડ કરવા માટે આ બેઝ રૂપે હોય છે. પછી જે સપાટી પર યંત્રણ કરવામાં આવેલ હોય તેના પર રહેલી ધાતુને ઓગાળીને પાર્ટ બનાવવામાં આવે છે. એનાથી સમયની બહુ બચત થાય છે.
એનું ઉત્તમ ઉદાહરણ છે ગોઠણનો કૃત્રિમ સાંધો. આ સાંધાના નીચેના હિસ્સાની પટ્ટીનું યંત્રણ પહેલા કરવામાં આવે છે અને પછી હિંજ પ્રિન્ટ કરવામાં આવે છે. ચિત્ર ક્ર. 11 માં દર્શાવ્યા મુજબ યંત્રણ કરેલ પ્લેટ ધાતુ છે. અસલમાં સંપર્ક પ્લેટ ટાઈટેનિયમની છે. અહીં બે અલગ અલગ ધાતુ છે. એક જ પાવડર બેડમાં બે અલગ અલગ ધાતુઓ નથી નાખી શકાતા, એટલે SLM તકનીકમાં પ્રથમ અડધો ભાગ પ્રિન્ટ કરવો પડે છે. પ્લેટનું જરૂરી યંત્રણ કરવું પડતું હોય છે, ત્યાર બાદ બીજા ભાગ પર પ્રિન્ટ કરી શકાય છે. પ્રિન્ટ કરવામાં આવેલ ભાગની જાડાઈ 0.1 મિમી. અથવા 0.2 મિમી. જેટલી અલ્પ હોઈ શકે છે. જ્યારે એક જ મૉડેલમાં બે પ્રકારના ધાતુ હોય ત્યારે સૉફ્ટવેઅર આ જાણકારી પ્રવિષ્ટ કરી શકાય છે તથા બેઝ મટીરિયલનું પૅરામીટર તથા એના પર પ્રિન્ટ થનાર ધાતુના ફ્યુઝિંગ પૅરામીટર, કોટિંગની જાડાઈ વગેરે બાબતોનું વ્યવસ્થાપન આ સૉફ્ટવેઅર દ્વારા કરવામાં આવે છે. એ માત્રામાં લેઝર બીમની તીવ્રતા (ઇન્ટેન્સિટી) નિર્ધારિત કરવામાં આવે છે.
પાવડર બેડ મશીનની પાવડર વ્યવસ્થાપન પ્રણાલી
પાવડર વ્યવસ્થાપન પ્રણાલી, મશીનમાં વપરાતી રીપ્લગ પ્રણાલીનો જ હિસ્સો છે. ધાતુનો પાવડર, લિફ્ટિંગ પ્રણાલી દ્વારા પાવડરની ટાંકીના કાર્યક્ષેત્રમાં લાવવામાં આવે છે.
ધારી લો કે શરૂઆતમાં જ ટાઈટેનિયમની કાર્યવસ્તુ પ્રિન્ટ કરવામાં આવી હોય અને પછીની કાર્યવસ્તુ એલ્યુમિનિયમમાંથી બનાવવાની હોય, તો પૂરા મશીનને સાફ કરી અગાઉ ઉપયોગમાં લેવાયેલ પાવડરનો દરેક કણ બહાર કાઢી તદ્દન સાફ કરવું જરૂરી હોય છે. આ પૂર્ણ પ્રક્રિયામાં એક થી બે દિવસ લાગે છે. પરંતુ રીપ્લગ પેટન્ટેડ તકનીકની (ચિત્ર ક્ર. 12) મદદથી આ કામ બે કલાકની અંદર જ પૂર્ણ થઈ જાય છે. ગ્રાહક પાસે એક થી વધુ રીપ્લગ યુનિટ હોય તો મટીરિયલ ઝડપથી બદલી શકાય છે. એનાથી મશીનનો ઉપયોગ ઈચ્છાનુસાર કરી શકાય છે. એ માટે દરેક ધાતુના પાવડર માટે અલગ અલગ કાર્ટ્રિજ રાખવું પડે છે. લેઝર ફ્યુઝનના ક્ષેત્રમાં પાસે રહેલા પાવડરના કણોનો આકાર તથા એના ગુણધર્મ બદલાઈ જાય છે. જો આપણે 20 માઈક્રોન આકારના પાવડરનો ઉપયોગ કર્યો હોય તો એ ક્ષેત્રમાં બચેલ પાવડરનો આકાર 150 માઈક્રોન હોય શકે છે. આ પાવડર રીપ્લગ યુનિટના રિસાઈકલ કરેલ ભાગની નજીક આવતા ત્યાં બેસાડવામાં આવેલ અલ્ટ્રાસોનિક સીવિંગ યુનિટ દ્વારા માત્ર 20 માઈક્રોનનો પાવડર બીજી વાર ઉપયોગમાં લેવા માટે ફરીવાર ટાંકીમાં મોકલાય છે. ઉષ્માના પ્રભાવથી આ પાવડરના ગુણોમાં બદલાવ આવી શકે છે. વ્યર્થ થઇ ગયેલ પાવડર ફરીથી એકત્ર કરવામાં આવે છે અને લગભગ 98% જેટલો પાવડર ફરી પ્રાપ્ત કરી લેવામાં આવે છે.
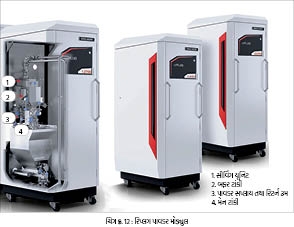
ડી.એમ.જી. મોરીએ ‘ઑપ્ટોમૅટ’ સૉફ્ટવેઅર બનાવેલ છે. જેમાં ફરી મેળવેલ પાવડર માટે અલગ અલગ પ્રોસેસ પૅરામીટર નિશ્ચિત કરવામાં આવે છે, જેથી અંતિમ કાર્યવસ્તુની ગુણવતા પર કોઈ પ્રભાવ ન પડે. આ સૉફ્ટવેઅર દરેક વખતે પ્રોસેસ પૅરામીટરમાં બદલાવ કર્યા કરે છે. એટલે શુદ્ધ પાવડરના પ્રથમ ઉપયોગથી લઈને પછી જો એનો જ 10 વાર ઉપયોગ કરવામાં આવે તો પણ મૂળ પાવડરના પ્રથમ તથા અંતિમ ઉપયોગ, આમ તમામ ઉપયોગ વખતે બનેલ કાર્યવસ્તુની ગુણવતા સમાન હોય છે.