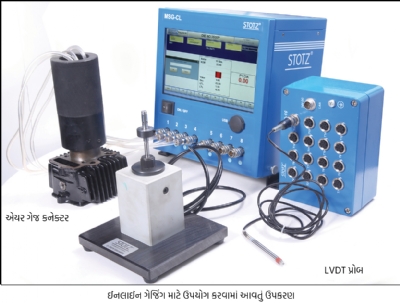
ફૅકટરીમાં પ્રચલિત નિરીક્ષણ પ્રક્રિયા હેઠળ, કામ દરમિયાન અને કામ પછી ઑપરેટરે અથવા તો ગુણવત્તા નિયંત્રણ વિભાગના કર્મચારીએ, પાર્ટની ચકાસણી કરવી જરૂરી હોય છે. પાર્ટના ડ્રૉઈંગ મુજબ અપેક્ષિત પરિમાણોની સરખામણીમાં વાસ્તવિક પરિમાણોની નોંધણી કરવી જરૂરી હોય છે. જો માપમાં ફર્ક પડી રહ્યો હોય, તો એના પર પણ નજર રાખી યંત્રણની પદ્ધતિમાં યોગ્ય બદલાવ કરવો પડતો હોય છે. એમાં ઘણીવાર નોંધાયું છે કે ચકાસણી કરનાર ઉપકરણો (જેમ કે ગેજ) જો મશીનથી દૂર હોય, તો એક બૅચ પૂર્ણ થયા બાદ એ બૅચના સેમ્પલ લઈને અથવા તો જો નાની બૅચ હોય તો પૂર્ણ બૅચ લઇ જઈને એની ચકાસણી કરવામાં, અને ત્યાર બાદ જે ખામી ધ્યાનમાં આવી હોય, તેને દૂર કરવા માટે મશીનમાં જરૂરી ફેરફાર કરવામાં ઘણો વિલંબ થાય છે. અને ત્યાં સુધીમાં તો મશીન પર કેટલાક પાર્ટ તૈયાર થઈ ગયા હોય છે. એનો અર્થ એ કે સમયસર કાર્યવાહી ન થવાના કારણે બૅચમાં ખરાબ પાર્ટની સંખ્યા અપેક્ષા કરતાં વધુ રહતી હતી. એ ટાળવા માટે, જ્યાં પાર્ટનું નિર્માણ થતું હોય, એ સ્થાન પર જ, ઑપરેટર તેની તપાસ કરે, જરૂરી પરિમાણોની નોંધણી કરે અને એ અનુસાર મશીનના સેટિંગમાં સુધારા વધારા કરે, તો ખોટા પાર્ટનું ઉત્પાદન બંધ થઈ જશે અને નુકસાન બચી જશે. એટલે, પ્રોસેસમાં જે પણ સુધારા કરવાના હોય, તે તરત જ અને ત્યાંને ત્યાં જ, કરવાથી બાકીના પાર્ટનું નિર્માણ ચોકસાઈ સાથે થશે. આ પ્રક્રિયાને 'ઇનલાઈન ગેજિંગ' કહેવામાં આવે છે. અમારી કંપની 'સુમૅક્સ' આ ઇનલાઈન ગેજિંગનો વધુમાં વધુ ઉપયોગ કરનાર ઉદ્યોગોમાંથી એક છે.
ઇનલાઈન ગેજિંગની કલ્પના અને અમલ અમારા ગ્રાહકો, મોટાભાગે ઑટોમેટિવ કંપનીઓને પાર્ટ સપ્લાય કરે છે. એટલા માટે ઑટોમેટિવ કંપનીઓને લાગુ પડતા સ્ટૅન્ડર્ડ મુજબ (અગાઉ જે QS, TS હતા; હવે IATF 16949 છે) ઉત્પાદનની ગુણવત્તા જાળવી રાખવી પડતી હોય છે. આમાં પ્રક્રિયા પર જરૂરી નિયંત્રણ મેળવવા માટે ઉત્પાદન પ્રક્રિયાનો સ્ટેટિસ્ટિકલ પ્રોસેસ કેપેબિલિટી સ્ટડી (SPC) કરાય છે.
અગાઉના સમયમાં ઑપરેટર જ પાર્ટનું પરીક્ષણ (ઇન્સ્પેકશન) કરતા હતાં. પરીક્ષણ પછી ગેજનું રીડિંગ કાગળ પર લખવામાં આવતું હતું, ત્યાર પછી એ યાદી ગુણવત્તા વિભાગને મોકલવામાં આવતી. ગુણવત્તા વિભાગના કર્મચારીઓ એ માહિતી એક્સેલ શીટમાં એન્ટર કરી કમ્પ્યૂટરમાં સાચવી રાખતા હતા. આ તમામ જાણકારીની એન્ટ્રી કર્યા બાદ પ્રોસેસ કેપેબિલિટી નિશ્ચિત કરવામાં આવતી હતી. ઑપરેટર દ્વારા પહેલા માપ લેવામાં આવતું, એની નોંધણી કરવામાં આવતી, ત્યાર બાદ રેખાકૃતિ (મશીન ડ્રૉઇંગ) બનતી, શૉપ ફ્લોર પર રન ચાર્ટ તૈયાર કરવો, દરેક એસ.પી.સી.ની ગણના કરવી, આ તમામ પ્રક્રિયાઓમાં ઘણો સમય લાગતો હતો. જે પણ વાસ્તવિક પરિમાણો પ્રાપ્ત થયા હોય, તેને માપી કોષ્ટકમાં એન્ટ્રી કરવાની જવાબદારી ઑપરેટરને જ સોંપવામાં આવતી. આથી ઉત્પાદકતા ઘટતી હતી. એ કારણે એ સ્થાને કોઈ પ્રશિક્ષિત, કુશળ, ઑપરેટરની જરૂરત હોવાનું પ્રતિત થવા લાગ્યું. જેમ જેમ વિદેશી ગ્રાહકો ભારતમાં આવવા લાગ્યા, આ સમસ્યા અત્યંત ગંભીર સ્વરૂપ લેવા લાગી. કેમકે ઑપરેટર લખતી વખતે, કોષ્ટક બનાવતી વખતે ડ્રૉઇંગ અનુસાર અનુમાનિત અંક એન્ટર તો કરતા હોય છે, પરંતુ તેણે એ માપ ચોકસાઈપૂર્વક જ લીધું હોય તેની કોઈ ખાતરી ન હતી. લખેલી માહિતી સાચી હોય એમ જ ગ્રાહક માની લેતા હોય છે. એટલે જો લિખિત રિપોર્ટ અને વાસ્તવિક માપમાં તફાવત ન હોય, તો આ પ્રક્રિયાની વિશ્વસનીયતામાં વધારો થાય છે. આ સંદર્ભે આ અત્યંત મહત્ત્વપૂર્ણ બાબત છે. અમે ઘણાં એક્સિબિશનમાં વિદેશી ઉપકરણો જોયા. અમે એ બાબત નોંધી કે ઑપરેટર, પાર્ટમાં ગેજ મૂકતાની સાથે જ એ જાણકારી કમ્પ્યૂટરમાં એન્ટર થાય છે. આમ આ જાણકારી એસ.પી.સી. માટે સતત રેકોર્ડ કરવામાં આવે છે. એના કોષ્ટક પણ બનાવવામાં આવે છે. આ જોઇને અમે અમારી ફૅકટરી માટે એ જ પ્રકારનું આધુનિક ઉપકરણ ખરીદવાનો નિર્ણય કર્યો.
શૉપ ફ્લોઅર પર અમે ઉચ્ચ ગુણવત્તા અને ચુસ્ત આકારનું ઉપકરણ વાપરીએ છીએ. આ ઉપકરણ માત્ર એસ.પી.સી. પરીક્ષણ જ નથી કરતું, પણ મશીનમાં સુધારા (કરેકશન) કરવા માટે આદેશ પણ આપે છે. આજકાલ આ પ્રોસેસ કેપેબિલિટી ઑનલાઈન થતી હોય છે. જે ક્ષણે માપ લેવામાં આવે છે, તે જ ક્ષણે સંકેત મળે છે. એ વખતે જો કોઈ ખામી અથવા દોષ હોય, તો ગુણવત્તા વિભાગને તરત જ જાણ કરવામાં આવે છે, જેમ કે કોઈ સમસ્યા છે અથવા મશીન બંધ કરવુ પડશે વગેરે.
કોઈ પાર્ટનું પરીક્ષણ કરવું હોય અને એ સંબંધે ઑફસેટમાં કોઈ ફેરફાર કરવા હોય, તો એ આપમેળે જ થઇ જાય છે અને એના પૅરામીટર આપોઆપ રેકૉર્ડ થઇ જાય છે. કોઈ પણ પાર્ટનું જે પણ રીડિંગ આપણને મળે, તે અનુસાર પછીના પાર્ટના નિર્માણમાં જરૂરી સુધારા કરી લેવામાં આવે છે. આ એક સતત પ્રક્રિયા હોય છે. આ ઑનલાઈન પ્રોસેસ કૅપેબિલિટી પૂર્વે Cpk 1.2 ની આસપાસ પહોંચતું હતું પણ ગ્રાહકોની માંગ ઓછામાં ઓછી 1.33 હતી. કુલ 50 માંથી જો 1 પણ પાર્ટ ટૉલરન્સ સીમા મર્યાદાની બહાર જાય, તો અપેક્ષિત Cpk મળતું ન હતું. પણ હવે આ પરિસ્થિતિ બદલાઇ ગઈ છે. હવે અમે 7 થી પણ વધુ Cpk મેળવી શકીએ છીએ. આટલી ઉચ્ચ ગુણવત્તાનું Cpk જોઇને ઘણાં લોકોને લાગે છે, કે આ રીડિંગ ખોટા હશે. પછી અમે તેમને વાસ્તવિક રીતે દર્શાવીએ છીએ. અમારા ઉત્પાદનો ગ્રાહકની અપેક્ષાથી ખરેખર વધુ ગુણવત્તાના હોય છે. હકીકત એ છે કે છેલ્લા ત્રણ વર્ષોમાં અમને અમારા ગ્રાહકો તરફથી કોઈપણ ફરિયાદ નથી મળી.
કેસ સ્ટડી 1 ઇન લાઈન ગેજિંગની અલગ અલગ પદ્ધતિઓ હોય છે. એમાંથી એક પદ્ધતિ આ કેસ સ્ટડીમાં દર્શાવવામાં આવી છે. આ પદ્ધતિ પ્રમાણે 100% કાર્યવસ્તુનું પરીક્ષણ કરવામાં આવશે અને તેને અનુસરી જરૂરી ફેરફાર કરવામાં આવશે. જો ઉચિત બદલાવ ન કરવામાં આવે, તો મશીન શરુ જ નહિ થાય, એવી ઇન્ટરલૉકની સુવિધા પણ આ પદ્ધતિમાં આપેલ છે.
તાપમાનમાં થનાર ફેરફારને કારણે એક પાર્ટના માપમાં બદલાવ થઇ રહ્યો હતો. સવારે, બપોરે, સાંજે અને રાત્રે, એવા અલગ અલગ સમયે, અલગ અલગ પરિમાણો નોંધાતા હતા, એક સમાન પરિમાણ મળતા ન હતા. અમે મશીનના પ્રોગ્રામ વડે તેમાં સુધારા કરી રહ્યા હતા, પણ ઑફસેટમાં સુધારા કરવામાં આવી રહ્યાં ન હતા. પ્રોગ્રામમાં સુધારા તથા રિપેરની જરૂર હતી. 100% પાર્ટનું પરીક્ષણ શરુ થવાને સમયે અમે તપાસ ઉપકરણમાં (ઇન્સ્ટ્રુમેન્ટ) જ એવી સુવિધા આપી, કે જો પાર્ટમાં કોઈ ફર્ક જણાય, તો મશીનને તરત જ સૂચના આપવામાં આવે અને જરૂરી ફેરફાર કરીને જ આગળનું ઉત્પાદન શરુ થઇ શકે.
દરેક પાર્ટના યંત્રણ બાદ કયા પૅરામીટર પર ધ્યાન દેવું જરૂરી છે, એ બાબતની સૂચનાઓ મશીનના પ્રોગ્રામમાં જ સમાવિષ્ટ છે. સાથે જ એ પૅરામીટરનો સંદર્ભ લઈ, આગળના કાર્ય અંગેની સૂચનાઓ આપવાની સુવિધા પણ કરાઈ છે. જો ઑપરેટર કોઈ પાર્ટની ચકાસણી ન કરે, તો મશીન એ પછીના કામ અંગેની સૂચનાનું પાલન નથી કરતું, પરિણામે મશીનનું કામ અટકી જાય છે. આનાથી જરૂરી માપન કરવાનું કાર્ય આપમેળે જ થવા લાગ્યું, મશીન રોકાયા વિના ચાલવાની પ્રક્રિયા સક્ષમ હોવા છતાં, ઑપરેટર દ્વારા થનારી તપાસ અનિવાર્ય બની ગઈ.
કેસ સ્ટડી 2 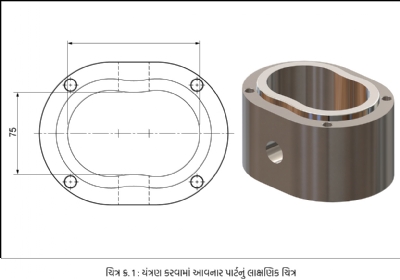
અમારી પાસેના એક પાર્ટના (ચિત્ર ક્ર. 1) યંત્રણ કરવાના એક ભાગની પહોળાઈ 75 મિમી. અને લંબાઈ 115 મિમી. હતી. આ બન્ને માપનમાં 20 માઈક્રૉનનું ટૉલરન્સ છે. જ્યારે એન્ડ મિલ દ્વારા પ્રોફાઈલ યંત્રણ કરવામાં આવે છે, ત્યારે એ વ્યાસ માટે કટર કમ્પેન્સેશન એક જ હોય છે. તેથી જેટલું કમ્પેન્સેશન પહોળાઈમાં હોય છે, એટલું જ કમ્પેન્સેશન લંબાઈમાં પણ કરવામાં આવે છે. કેમકે લંબાઈ (115) પહોળાઈ (75) કરતા લગભગ દોઢ ગણી છે, એના તાપમાનના વિસ્તરણનો ગુણાંક (કોઇફિશન્ટ) બદલાઈ જાય છે. જો પહોળાઈ 15 માઈક્રૉન જેટલી વધી જાય, તો લંબાઈ લગભગ 35 માઈક્રૉન જેટલી વધી જાય છે. એ પ્રકારે એમાં બદલાવ થઇ જાય છે. બન્ને પૅરામીટર માટે એક જ કમ્પેન્સેશન ન આપી શકાય. એની પ્રોફાઈલ એક ત્રાંસા ઑબ્લૉંગ સ્લૉટ સમાન હોય છે. એટલે જો એમાં 15 માઈક્રૉનનો સુધાર કરવામાં આવે, તો પહોળાઈ કમ્પેન્સેટ થઇ જાય છે અને લંબાઈમાં 35 માઈક્રૉનનું કમ્પેન્સેશન કરવાની જરૂર પડે છે. આ ન્યાયે 35– 15 = 20 માઈક્રૉનનો વાસ્તવિક બદલાવ અમારે કરવો પડે છે. એ માટે અમે એની ત્રિજ્યાનું મધ્ય બિંદુ દરેક માટે 10 માઈક્રૉન જેટલું અંદર ખેંચેલ છે. એમ કરવાથી એ કમ્પેન્સેટ થઇ ગયું. અમારી મશીનમાં આ કમ્પેન્સેશન માપન અનુસાર આપમેળે જ થાય છે. આ પહેલાં દરેક શિફ્ટમાં એક એન્જિનિયરને કોઈ ફર્ક (વેરીએશન) છે કે નહિ, એ બન્ને તરફથી તપાસવા માટે, પ્રત્યક્ષ રૂપે મશીન પાસે જવું પડતું હતું.
આ મશીન પર એક સાથે બે પાર્ટનું યંત્રણ થઇ શકે છે. બન્ને પાર્ટની હાર્ડનેસ (કઠણપણું) અલગ અલગ હોઈ શકે છે. એટલા માટે એક પાર્ટના રીડિંગ અનુસાર કરવામાં આવેલ મશીન કરેકશન, બીજા પાર્ટને માટે લાગુ ન પડે. તો એ વખતે બન્ને પાર્ટનું રીડિંગ લઇ એના સરેરાશ મૂલ્યનું કૉમ્બિનેશન મશીનમાં ફીડ કરવામાં આવે છે. મશીનના પ્રોગ્રામમાં ફેરફાર થઇ શકે છે, આ એક મહત્ત્વપૂર્ણ લાભ છે. કેમકે રિજેકશન ટાળવા માટે, પ્રોફાઈલની લંબાઈ અને પહોળાઈમાં માત્ર 20 માઈક્રૉનનું ટૉલરન્સ હોય છે, માઈક્રૉન સ્તરના નજીવા ફરકને કારણે પણ પાર્ટ રિજેક્ટ થઇ શકે છે. તેની સાથે જે પણ ફેરફાર કરવા પડતા હોય તે બધા શું એક સમાન છે એની ચોકસાઈપૂર્વક તપાસ કરી જો એ એક સમાન ન હોય, તો પ્રોગ્રામમાં કેન્દ્ર (સેન્ટર) સેટ કરવામાં આવે છે. હવે અમે પૅરામેટ્રિકલ પ્રોગ્રામિંગ કરીએ છીએ, જેના માટે અમારા ગેજમાંથી જ ઈનપુટ મળે છે. આ રીતે પાર્ટ બનાવીને અમારો અનુભવ એ રહ્યો છે, કે Cpk 1.22 થી 7 સુધી વધેલ છે. એ મુજબ કામ કરવાથી કાર્યમાં સુસંગતતા રાખવામાં મદદ મળી, હવે કુશળ ઑપરેટર પર નિર્ભર રહેવાની જરૂરત નથી રહી, ટૂલના ઘસારાથી પરિમાણોમાં આવતો ફરક અટકી ગયો. અગાઉ નિશ્ચિત સંખ્યામાં પાર્ટ બનાવ્યા બાદ ટૂલ ઇન્સર્ટ બદલવામાં આવતું. એ પ્રક્રિયામાં કેટલાક સારા ઇન્સર્ટ વેડફાઈ જતા હતા. હવે દરેક પાર્ટનું માપ ચોકસાઇથી લેવામાં આવે છે, એટલે ઇન્સર્ટ ત્યારે જ બદલવામાં આવે છે, જ્યારે ખરેખર જરૂરી હોય. આમ ઑપરેટરના અનુભવને આધારે અથવા અનુમાનને કારણે કરવામાં આવતો ઇન્સર્ટનો બદલાવ બંધ થઈ જવાથી ઇન્સર્ટના ખર્ચમાં પણ બચત થઈ ગઈ.
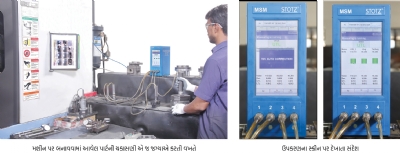
કેસ સ્ટડી 3આ મશીન પર રોબોની મદદથી પાર્ટને હઁડલ કરવામાં આવે છે. અહી મશીનમાં જ ઈનલાઈન ગેજ (ચિત્ર ક્ર. 2) મૂકવામાં આવે છે. અને તેને બહારથી મેઝરમેન્ટ રેકોર્ડર જોડી મશીન સાથે સંકળાઈ લેવામાં આવે છે. જરૂરત પડે ત્યારે ગેજ આગળ આવી પાર્ટનું પરીક્ષણ કરે છે અને માપ યોગ્ય હોય ત્યારે જ પાર્ટ મશીનમાંથી બહાર આવે છે. અમે એવા ઇન્ટરલૉક લગાડ્યા છે, કે જો માપમાં ફર્ક હોય તો મશીનના પ્રોગ્રામમાં જરૂરી બદલાવ કર્યા વિના પાર્ટ બહાર જ ન આવી શકે.
એનો અર્થ એ કે માપ જો નિયતથી ઓછું હોય, તો પાર્ટ રિજેક્ટ થઇ જશે અને પ્રોગ્રામમાં ફેરફાર કર્યા બાદ જ પછીના પાર્ટ પર કામ કરવામાં આવશે. અને જો માપ નિયત અથવા અપેક્ષિત કરતા વધુ હોય, તો પણ મશીનના પ્રોગ્રામમાં જરૂરી બદલાવ કરીને જ પાર્ટ બહાર કાઢી શકાય છે.
માપનની ચોકસાઈ કાયમ રાખવા અમે શું કર્યું? અમે અમારી પ્રક્રિયામાં અમુક પગલાં અનિવાર્ય કરેલ છે. દા.ત. ઑપરેટર જ્યાં સુધી તમામ જરૂરી ચકાસણીઓ પૂરી ન કરે, ત્યાં સુધી પ્રક્રિયા આગળ નથી વધતી. તેથી રેકોર્ડ બનાવનાર વ્યક્તિ દ્વારા થનારી ભૂલો (મૅન્યુઅલ એરર) લગભગ ખતમ જ થઈ ગઈ. આ સાધનની પરિશુદ્ધતા 0.01 માઈક્રૉન છે. આ તપાસ કરવા અમે અપ્રાઈઝર પદ્ધતિનો ઉપયોગ કર્યો. જેમ કે એક ગેજ R&R (રિપિટેબિલિટી અને રિપ્રોડ્યૂસિબિલિટી) કરવા માટે 3 અપ્રાઈઝર જરૂરી છે. એમાંથી એક તો ઑપરેટર હોઈ શકે. બીજી વ્યક્તિ એન્જિનિયર અને ત્રીજી વ્યક્તિ કલાર્ક હોઈ શકે છે. ત્રણેય દ્વારા કરવામાં આવેલ માપના પરિણામ એકસરખા જ હોવા જોઈએ. જો એ એકસરખા હોય, તો એ સાબિત થાય છે કે ગેજમાં કોઈ ખામી નથી. જો એમાંથી કોઈપણ બે રેકોર્ડમાં વધુમાં વધુ 0.04 µm, 0.05 µm નો ફર્ક હોય, તો પણ એ ફર્ક 1 માઈક્રૉનથી ઓછો હોવાને કારણે, એ ગેજ પરિશુદ્ધ જ ગણવામાં આવે છે.
ઈનલાઈન ગેજિંગ માટે અમે STOTZ કંપનીનું MSM ઉપકરણ વાપરીએ છીએ. પ્રક્રિયા અનુસાર ઉપકરણ બદલવામાં નથી આવતું. અસલમાં આ બધા સ્ટૅન્ડર્ડ ઉપકરણો જ હોય છે. પ્રોગ્રામ કર્યા અનુસાર પ્લગ ઇન ગેજ બદલીને આપ પ્રોગ્રામ ફરી રન કરી શકો છો. એના સેટિંગ પણ ઝડપથી બદલી શકાય છે. અમુક ગેજ કનેક્શન આગળની તરફ હોય છે, જ્યારે અમુક પાછળની તરફ. આગળની તરફ એયર ગેજ અથવા LVDT ગેજ હોય છે. એ પણ જરૂરિયાત અનુસાર નિર્ધારિત થાય છે. પણ પાછળની તરફ માત્ર LVDT ગેજનો જ ઉપયોગ કરવામાં આવે છે. આ ગેજનું આઉટપુટ આ ઉપકરણ સાથે જોડવામાં આવે છે અને ઉપકરણનું આઉટપુટ મશીનમાં આપવામાં આવે છે. આ બધું ડિજિટલ ઑટો આઉટપુટ પોર્ટ દ્વારા થાય છે. આ પોર્ટ મશીનને ફીડબૅક આપે છે. આપણે તેને નિયંત્રક (કંટ્રોલર) સાથે અથવા તો કોઈપણ ઈચ્છિત જગ્યા સાથે જોડી શકીએ છીએ. loT જેવી નવી ટૅક્નોલૉજી માટે આ ઉપકરણ પૂરક છે. આ પોર્ટ દ્વારા માહિતી કલાઉડ પર પણ મોકલી શકાય છે. સૌ પ્રથમ એની માસ્ટર વેલ્યૂ નિર્ધારિત કરવામાં આવે છે. એના માટે એ ઉપકરણમાં પ્રોગ્રામ બનાવવો પડે છે. જયારે ગેજ જોડવામાં આવે, ત્યારે પ્રથમ આવનારી માસ્ટર વેલ્યૂ આ ઉપકરણમાં પ્રવિષ્ટ કરવામાં આવે છે. આને લિંક વેલ્યૂ કહેવામાં આવે છે. માસ્ટર પાર્ટની તપાસ કરતી વખતે માની લો કે 1 માઈક્રૉનથી વધુનો ફર્ક છે અને ઉપકરણ કૅલિબ્રેટ કરવાનું છે. જેમ ગેજમાં ઘસારો થાય, ઉપકરણમાં સંકેતની ઘંટી (એલાર્મ) વાગવા લાગે છે. એનો અર્થ એ કે ગેજ કૅલિબ્રેટ કરો અથવા તો ન વાપરો. આવા તો ઘણા લાભ તેને લીધે પ્રાપ્ત થાય છે. ગ્રાહકની જરૂરિયાત અનુસાર મશીનમાં પ્રોગ્રામિંગ કરી શકાય છે. મલ્ટી ગેજિંગના ઉપયોગથી, એક જ ગેજ સાથે મલ્ટિપલ ફીચર પણ એક સાથે માપી શકાય છે. જ્યારે સ્થિતિ નિયંત્રણની બહાર થઇ જાય ત્યારે સંબંધિત વ્યક્તિને તમે ઈમેઈલ પણ કરી શકો છો. આવી ઘણી સુવિધાઓ એમાં આપવામાં આવી છે. કલાઉડ પર જાણકારી મોકલવી હોય તો LAN, USB પોર્ટ જરૂરી છે. RS232 પોર્ટ પણ છે, જેનો ઉપયોગ માત્ર માહિતીની આપ લે માટે કરી શકાય છે. અમારી પાસે આવા 11 ઉપકરણ છે.
હું અહીં જરૂરથી ઉલ્લેખ કરવા માંગું છું કે ઝીરો ડીફેક્ટ, પ્રગતિ તરફ સદા અગ્રેસર, ક્લીન ઇન પીસ (સી.આઈ.પી.) અને ગ્રાહકનો સંતોષ આ કાર્યપ્રણાલી માટે અમારી ટીમ હંમેશા કોશિશ કરતી રહેશે.