કાર્યવસ્તુનું અંતિમ અપેક્ષિત માપ મેળવવા અને ઇચ્છિત ફિનિશ પ્રાપ્ત કરવા, વિશેષ મશીનિંગ પ્રક્રિયાઓ કરવાની જોગવાઈ કરવામાં આવે છે. આ લેખમાં આમાંથી એક, એટલે લૅપિંગ પ્રક્રિયા વિષે આપણે જાણીશું. કાર્યવસ્તુની જાડાઈ, સમતલતા તથા સપાટીની ફિનિશિંગના ઈચ્છિત ટૉલરન્સ પ્રાપ્ત કરવાના ઉદ્દેશ્યથી કાર્યવસ્તુના (અથવા નમૂનો) સમતલ સપાટીમાંથી જરૂરીયાત મુજબનું મટીરિયલ લૅપિંગ પ્રક્રિયા દ્વારા ચોકસાઇપૂર્વક કાઢવામાં આવે છે. લૅપિંગ અને પૉલિશિંગ પ્રક્રિયાઓ, અલગ અલગ પ્રકારના મટીરિયલ અને ઍપ્લિકેશન માટે ઉપયોગમાં લેવામાં આવે છે). આમાં અલગ અલગ પ્રકારના ધાતુ, કાંચ, ઑપ્ટિક્સ અને સિરેમિક્સનો પણ સમાવેશ હોય છે.
ફૅમિંગ પ્રક્રિયામાં, ઍબ્રેઝિવ્હ કણો ધરાવતી સ્લરીને પ્લેટમાં એમ્બેડ ન થવા દઈ સ્વતંત્ર રીતે વહેવા દેવામાં આવે છે. પણ લૅપિંગ પ્રક્રિયામાં અમુક ઍબ્રેઝિવ્હ કણો પ્લેટમાં એમ્બેડ થઇ જાય છે અને બાકી બચેલા કણો જ સ્વતંત્ર રીતે વહે છે. બંને પ્રકારના કણો કટિંગ ટૂલના રૂપે જ કાર્ય કરે છે. ફૅમિંગ પ્રક્રિયાની તુલનામાં, લૅપિંગ પ્રક્રિયામાં વધારાનું મટીરિયલ (સ્ટૉક) બહાર કાઢવાની ગતિ ખૂબ ઓછી હોય છે અને સપાટીના ફિનિશના મૂલ્ય, ખાસ કરીને Rz પર, અચૂક નિયંત્રણ હોય છે.
લૅપિંગ પ્રક્રિયામાં, લગભગ 200 થી 220 BHN કઠિનતા (હાર્ડનેસ) વાળી કાસ્ટ આયર્નની એક પ્લેટ ઉપયોગમાં લેવાય છે. આમાં ઍબ્રેઝિવ્હના કણો ભરાઈ જાય છે (ઈમ્પ્રિગ્નેટ) અને એ પ્લેટનો ઉપયોગ લૅપિંગ ટૂલની જેમ કરવામાં આવે છે. લૅપિંગ પ્રક્રિયામાં મટિરિયલ ચોકસાઈપૂર્વક તથા નિયંત્રિત રીતે કાઢવામાં આવતું હોવાથી એ ફાયદાકારક નીવડે છે. ફૅમિંગની જેમ જ લૅપિંગ પ્રક્રિયામાં પણ કાર્યવસ્તુ કૅરિયર પૉકેટમાં રાખવામાં આવતી હોવાથી તેનાથી તણાવ થતો નથી.
એક બાજૂની લૅપિંગ (SSM)
પ્લેટ પર સ્થિત કૅરિયર રિંગમાં કાર્યવસ્તુ એ રીતે મુકવામાં આવે છે, કે જે સપાટીની લૅપિંગ કરવાની હોય તે સપાટી લૅપિંગ પ્રક્રિયામાં પ્લેટની સામે આવે. આ કૅરિયર રિંગ, કાર્યવસ્તુ અનુસાર બનાવવામાં આવે છે.
ચિત્ર ક્ર. 1 માં દર્શાવ્યા અનુસાર કાર્યવસ્તુને ક્યાંયથી પણ કસીને ન પકડી, લૅપિંગ પ્લેટની સપાટી પર ઘર્ષણ થાય, તે માટે તેને ઉપરથી દબાણ આપવામાં આવે છે. આ પ્રક્રિયા માટે ડેડ વેટ અથવા ન્યૂમૅટિક સિલિન્ડરનો ઉપયોગ કરવામાં આવે છે. કાર્યવસ્તુની જાડાઈ/ઊંચાઈમાં તફાવત હોવાને કારણે દબાણ કરવાવાળી પ્લેટ અને કાર્યવસ્તુમાં કુશનિંગ કરવા માટે વિશેષ પૅડ લગાડવામાં આવે છે. એના પર વજન/દબાણ મૂકવામાં આવે છે અને આ સઘળું કરતી વખતે કાર્યવસ્તુનું ક્ષેત્રફળ અને કુલ ઉપલબ્ધ ક્ષેત્રફળની ગણતરી કરીને એ અનુસાર વજન/દબાણનું મૂલ્ય નિર્ધારિત કરવામાં આવે છે. અમુક કાર્યવસ્તુઓ મશીનમાં લોડ કરતી વખતે એમને કૅરિયરની જરૂર પડતી હોય છે અને અમુક કાર્યવસ્તુઓને જરૂર નથી પડતી. કાર્યવસ્તુની રચના અને એની સપાટીના અપેક્ષિત ફિનિશ પર એ નક્કી કરવામાં આવે છે, કે કૅરિયરની જરૂર પડશે કે નહિ. મશીન શરુ કરતા પૂર્વે ઍબ્રેઝિવ્હ કણો અને પાણી/ઑઈલની સ્લરી બહાર આવી પ્લેટ પર ફેલાવા લાગે છે. આ માટે એક વિશેષ સમયગાળો નિશ્ચિત હોય છે. એ સમયગાળો પૂર્ણ થતાં જ પ્લેટ ફરવાનું શરુ થાય છે. મોટા મશીનોમાં સ્લરીને એકત્ર કરવા માટે એક સ્ટરર મોટર તથા પંપ હોય છે. નાના મશીનોમાં સ્લરીને એકત્ર કરવા માટે સ્ટરર મોટર નથી હોતી. ચાર રિંગની ગોઠવણ વાળી આ રચનામાં જ્યારે લૅપિંગ ચાલુ હોય, ત્યારે લૅપિંગ પ્લેટ, ફૉરવર્ડ તથા રિવર્સ બંને દિશાઓમાં ફેરવી શકાય છે. એના માટે પણ એક નિશ્ચિત સમયાવધિ નિર્ધારિત કરી એ બંનેનું હલનચલન કરવામાં આવે છે.
ત્રણ રિંગની રચનાવાળા મશીનમાં રિંગ એવી રીતે ગોઠવવામાં આવે છે, કે જેથી પ્લેટની સમતલતાના આધારે બાહ્ય અથવા આંતરિક વ્યાસ પર ઓવરહેંગ મળે. ઉદાહરણ તરીકે, જો લૅપપ્લેટ 800 મિમી. ની હોય અને એની સમતલતા 100 માઈક્રોન હોય તો કાર્યવસ્તુના 50 મિમી. ના વ્યાસ માટે 0.39 માઈક્રોનમાં લૅપિંગ કરવાથી એક સમતલ કાર્યવસ્તુ મળશે તેવી અપેક્ષા આપણે રાખી શકીએ. પણ જો કાર્યવસ્તુ 100 મિમી. ની હોય તો આપણે કાર્યવસ્તુની સમતલતા 1.56 માઈક્રોન જેટલી રાખવાની અપેક્ષા કરી શકીએ છીએ.
બંને તરફ લૅપિંગ કરનાર (DSM) મશીનનું વર્ણન
ફોર વે ડબલ સાઈડેડ લૅપિંગ મશીનનું વર્ણન), કોષ્ટક ક્ર. 1 માં આપેલ વિશિષ્ટ નામાભિધાન (નૉમેનક્લેચર) અનુસાર કરવામાં આવે છે.
આ મશીનની લૅપિંગ પ્લેટ, કૅરિયર પ્લેટ તથા રિંગનું એક રેખામાં હોવાની ખાતરી કરવા માટે, કેન્દ્રરેખાથી ડ્રાઈવ કરવામાં આવેલ ડ્રાઈવિંગ અસેમ્બ્લી ચિત્ર ક્ર. 2 માં દર્શાવવામાં આવી છે. બંને તરફથી લૅપિંગ કરનાર મશીનની પ્રક્રિયાને કલ્પનાત્મક રૂપે ચિત્ર ક્ર.3 માં દર્શાવવામાં આવેલ છે.
વાયુનું દબાણ અને સમયનું આયોજન
પ્રક્રિયા દરમિયાન લૅપિંગ પ્લેટ પર પડતું વાયુનું દબાણ અને કામના સમયગાળાનું આયોજન કરવું અત્યંત જરૂરી હોય છે. આ આયોજન ત્રણ તબક્કામાં હોય છે અને એને સંબંધિત ટાઈમર દ્વારા કરીને આ પ્રક્રિયાનું સેટઅપ તૈયાર કરવામાં આવે છે. લૅપિંગ માટે આવતી કાર્યવસ્તુઓની જાડાઈમાં જે કોઈ તફાવત હોય, તેને દૂર કરવા માટે પ્રારંભિક દબાણ P1 ઓછો રાખવામાં આવે છે. ઇચ્છિત, અપેક્ષા મુજબનો સ્ટૉક કાઢવા માટે P2 દબાણ અને સ્પાર્ક ઑફ સાઈકલ માટે P3 દબાણ (ચિત્ર ક્ર. 4) સેટ કરવામાં આવે છે. એ માટે લાગનારા સમયને ટાઈમરમાં T1, T2 અને T3 તરીકે સેટ કરવામાં આવે છે.
કાર્યવસ્તુની સમતલતા અને સમાંતરતા, બંને લૅપ પ્લેટના પ્રતિબિંબ હોય છે. કાર્યવસ્તુની સમતલ સપાટી મેળવવા માટે પ્લેટની સમતલતા પણ જાળવી રાખવી અત્યંત જરૂરી હોય છે. પ્લેટની સમતલતાનું કંડિશનિંગ કરવા માટે ઘણી બધી રીતો છે. DSM માં ફૉરવર્ડ/રિવર્સ પદ્ધતિના ઉપયોગથી પ્લેટનું કંડિશનિંગ કરી શકાય છે.
ચાલો હવે આપણે ઑટોમોટિવ પાવર સ્ટીઅરિંગ અસેમ્બ્લીમાં જે ઉપયોગમાં લેવામાં આવે છે તે સ્ટેટરનું ઉદાહરણ જોઈએ. પાવર સ્ટીઅરિંગ અસેમ્બ્લીમાં સ્ટેટર અને રોટરની જોડી પાવર સ્ટીઅરિંગના સહેલા તેમજ સરળ ઉપયોગ માટે અત્યંત અસરકારક હોય છે. એ માટે એમની સમતલતા, સપાટીનું ફિનિશ, સમાંતરતા, જાડાઈનું ટૉલરન્સ વગેરે તમામ મહત્ત્વના પૅરામીટર નિયંત્રણમાં રાખવા પડતા હોય છે, જેથી એને અન્ય કોઈપણ સ્ટેટર અને રોટર સાથે સરળતાથી અને ખાતરી લાયક રીતે બદલી શકાય.
અહીં દર્શાવવામાં આવેલ કાર્યવસ્તુનું મટિરિયલ 20MnCr5 છે. સામાન્ય રીતે આ કાર્યવસ્તુનો આકાર Ø82મિમી. x 13 મિમી. (જાડાઈ) હોય છે. બધી કાર્યવસ્તુઓના માપ નિર્દિષ્ટ ટોલરન્સમાં હોય તે જરૂરી છે. સાથે સાથે એ પણ જરૂરી છે કે બધા પાર્ટની એકબીજા સાથે સહેલાઈથી અદલાબદલી પણ થઇ શકે. લૅપિંગ માટે આવનારી કાર્યવસ્તુની જાડાઈ 13.4 મિમી. ± 0.02 મિમી. હોય છે. એને 13.39 ± 0.005 મિમી. સુધી ઘટાડવાની હોય છે. લૅપિંગ પૂર્વે, સરફેસ ગ્રાઈન્ડરનો ઉપયોગ કરીને કાર્યવસ્તુનું પ્રી-ગ્રાઇન્ડિંગ કરાવામાં આવે છે. પ્રથમ કરવામાં આવેલ પ્રક્રિયામાં સપાટી પર 0.8 માઈક્રોન Ra સુધીનું ફિનિશ મળે છે, જેને 0.2 માઈક્રોન Ra સુધી સુધારવું જરૂરી હોય છે. દરેક 7 કલાકની શિફ્ટમાં 600 કાર્યવસ્તુઓના લૅપિંગનો ટાર્ગેટ રાખવામાં આવે છે. બંને તરફની લૅપિંગ માટે કાર્યવસ્તુની સમાંતરતા 10 માઈક્રોન સુધીની હોય છે, જેમાં 2 માઈક્રોન સુધીનો સુધારો કરવાનું અપેક્ષિત હોય છે. અહીં ઉપયોગમાં લેવાયેલ મશીન સ્પીડફૅમ ડબલ સાઈડેડ લૅપિંગ મશીન મૉડલ 9B-5L છે. (ચિત્ર ક્ર. 5)
મશીનની પસંદગી
યોગ્ય આકારના મશીનની પસંદગીને અસર કરતા પરિબળો જોવા માટે આપણે સ્ટેટરનું ઉદાહરણ લઇશું.
1. જરૂરી ઉત્પાદન/કલાક : 256 કાર્યવસ્તુ
2. કારખાનાની કાર્યક્ષમતા : 85%
3. કાઢી નાંખવાનું મટિરિયલ : 10 માઈક્રૉન
4. લૅપિંગ પછી સપાટીનું જરૂરી ફિનિશ : 0.8 Ra, એના માટે જ SFBLAP 08 ની પસંદગી કરવામાં આવી છે.
5. સમતલતાનું ટૉલરન્સ : 3 માઈક્રૉનથી પણ ઓછું
6. સમાંતરતાનું ટૉલરન્સ : 2 માઇક્રૉનથી પણ ઓછું
7. CpK: ઓછામાં ઓછું 1.66
પ્રક્રિયાના અન્ય ઘટકોની પસંદગીને અસર કરતા પરિબળો
1. ઍબ્રેઝિવ્હની પસંદગી
વધુ સમય સુધી ધાર જાળવી રાખે, તેવી કટિંગ એજ મેળવવા માટે લૅપિંગમાં વાપરવામાં આવતા પ્રચલિત ઍબ્રેઝિવ્હ કણોનો આકાર સુક્ષ્મ બ્લૉક્સ જેવો હોય છે.
સામાન્ય રીતે ઉપયોગમાં લેવાતા ઍબ્રેઝિવ્હ
- બૉરૉન કાર્બાઈડ (B4C) : આ વાપરવાથી (ચિત્રક્ર. 6) મટીરિયલ અત્યંત ઝડપથી બહાર નીકળે છે, પણ કયારેક સપાટીના ફિનિશના મૂલ્ય પર, Rz ના અને તે કારણે Ra ના સંદર્ભમાં જતું કરવું પડતું હોય છે.
- સિલિકૉન કાર્બાઈડ (SiC) : આ વાપરવાથી મટીરિયલ મધ્યમ ગતિએ બહાર આવે છે. પણ Rz અને તેને કારણે Ra ના સંદર્ભે સપાટીના ફિનિશના મૂલ્ય પર વધુ નિયંત્રણ મળે છે. SiC કાળા અથવા લીલા સિલિકૉનના રૂપમાં મળે છે.
- ઍલ્યુમિનિયમ ઑક્સાઈડ (Al2O3): મટિરિયલ કાઢવાની આની ઝડપ તુલનામાં ઘણી ઓછી હોય છે. પણ Rz અને તેને કારણે Ra ના સંદર્ભમાં સપાટીના ફિનિશનું મુલ્ય ઘણું સારું હોય છે.
કોઈપણ હાલતમાં નિરંતર સારા પરિણામો મેળવવા દરેક ચાર્જમાં ઍબ્રેઝિવ્હ કણોનો આકાર, ઍબ્રેઝિવ્હના વિશિષ્ટ મૂલાધારી આકારના સંદર્ભમાં નિયંત્રિત હોવો અત્યંત જરૂરી છે. ઍબ્રેઝિવ્હના વિશિષ્ટ મૂલાધારી આકાર, 1 માઈક્રૉન કરતા પણ ઓછાં મૂલ્યથી લઈને 60 થી 80 માઈક્રૉન સુધીના હોય છે.
ઍબ્રેઝિવ્હના યોગ્ય પ્રકાર અને આકારની પસંદગી, લૅપિંગ પછીના જરૂરી સપાટીય ફિનિશના મૂલ્ય પર આધાર રાખે છે. સ્ટેટર પાર્ટ માટે લીલા રંગના સિલિકૉનનો ઉપયોગ કરવામાં આવે છે.
2. વાહકની પસંદગી
આ પૂર્ણ પ્રક્રિયા દરમિયાન, ઍબ્રેઝિવ્હ અને તેનું વાહક એક બીજા સાથે સારી રીતે ભળી ગયેલા હોવા જોઇયે. તેની ખાતરી કરવા માટે વાહકનું સસ્પેન્શન ઉત્તમ હોવું જરૂરી છે. સાથે જ એમાં મેળવવામાં આવેલ ઍબ્રેઝિવ્હના કણો ઘસાઈને બુઠ્ઠા થવાના કારણે કટિંગની ક્રિયા સારી ન થતી હોય, ત્યારે તે ઍબ્રેઝિવ્હ વાહકમાં થી અલગ કરીને તેને પાછું મેળવવાનું (રીક્લેમ) પણ સંભવ હોવું જોઈએ. વાહક્ને પાછું મેળવવાથી વસ્તુ દીઠ લૅપિંગના ખર્ચમાં ઘણો ફરક પડે છે. પાણી આધારિત વાહકમાં યોગ્ય ઘટકો હોવા જોઈએ, જેથી પ્રક્રિયા દરમિયાન વાહકના સંપર્કમાં આવનાર તમામ કાર્યવસ્તુઓમાં કાટ ન લાગે. સ્ટેટર માટે તેલપર આધારિત વાહકનો ઉપયોગ કરવામાં આવેલ છે.
3. સ્લરી તૈયાર કરવી
બે આવર્તન વચ્ચે અથવા તો બે શિફ્ટ વચ્ચેના સમયમાં જ્યારે મશીનનો ઉપયોગ ન થઇ રહ્યો હોય, ત્યારે પણ સ્લરી હલાવતા રહેવા માટે સ્ટરર મોટર તથા અસેમ્બ્લીયુક્ત યોગ્ય પ્રકારના સ્લરી પંપનો (ચિત્ર ક્ર. 7) ઉપયોગ કરવો અત્યંત જરૂરી છે.
આ ઉપરાંત, ખાસ કરીને પાણી આધારિત વાહકનો ઉપયોગ કરતી વખતે એ અત્યંત મહત્ત્વપૂર્ણ છે કે પાણીના સંપર્કમાં આવનારા પંપના પાર્ટની સલામતી સુનિશ્ચિત કરે તેવા સ્લરી પંપની પસંદગી કરવામાં આવે. સ્લરીમાં ઍબ્રેઝિવ્હની માત્રા પણ યોગ્ય પ્રમાણમાં હોય તે જરૂરી છે. એ જ પ્રકારે, સ્લરી અને મિશ્રણના યોગ્ય ગુણોત્તર તરફ ધ્યાન દેવું એટલું જ જરૂરી છે, જેથી ઉત્તમ કાર્યક્ષમતા પણ મળે તથા બચત પણ થાય.
DSM માં એક વાર ભરવામાં આવેલ સ્લરીને પૂર્વનિર્ધારિત સંખ્યાની કાર્યવસ્તુઓ પર જ ઉપયોગમાં લઇ શકાય છે. ત્યાર બાદ કાર્યક્ષમ યંત્રણ સુનિશ્ચિત કરવા માટે, જૂની સ્લરી કાઢી લઇ નવી સ્લરી ભરવામાં આવે છે. વપરાશમાં લઇ લીધેલ સ્લરીની અંદરના તેલ આધારિત વાહકનો ફરીથી ઉપયોગ કરવા માટે તેને ઑઈલ રિક્લેમ પ્રણાલીમાં લઈ જવી પડે.
4. કૅરિયરની પસંદગી
અમુક કાર્યવસ્તુઓ રિટેનિંગ રિંગમાં રાખવી શક્ય હોય તો પણ અનેક કાર્યવસ્તુઓ કૅરિયરમાં બનાવાયેલ પૉકેટમાં રાખવી જરૂરી હોય છે. લૅપિંગ પ્રક્રિયા દરમિયાન લૅપિંગ પ્લેટનું ઘર્ષણ એકસમાન થાય એ સુનિશ્ચિત કરવા માટે કૅરિયરની ગોઠવણ એક વિશિષ્ઠ પ્રકારની હોય તે જરુરી છે. કેસ સ્ટડીમાં સ્ટેટર માટે પાંદડાઓના આકારનું પૉકેટવાળું કૅરિયર ઉપયોગમાં લેવામાં આવ્યું છે.
5. અન્ય મશીન સેટિંગ પૅરામીટરની પસંદગી
અન્ય ઘણા બધા પૅરામીટર સેટ કરવાના હોય છે જેવા કે, પ્લેટનું R.P.M., રિટેનિંગ રિંગની ફરવાની દિશા, વાયુના દબાણની પસંદગી (પ્રારંભે ઓછું અને પછી થોડું વધુ દબાણ), દબાણને હિસાબે યોગ્ય ટાઈમ સેટિંગની પસંદગી વગેરે.
DSM માં લૅપિંગ થયા બાદ કાર્યવસ્તુની સમતલતા અને સપાટીના ફિનિશનું માપન કરવામાં આવે છે. 100 મિમી. કૅરિયર વ્યાસથી લઈને 450 મિમી. કૅરિયર વ્યાસના મશીન ઉપલબ્ધ છે.
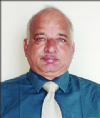
પ્રફુલ ગોવંડે
મૅનેજમેન્ટ ડિરેકટર, સ્પીડફૅમ (ઇન્ડિયા) પ્રા.લિ.
9833581046
[email protected]
પ્રફુલ ગોવંડે મેકૅનિકલ એન્જિનિયર છે અને આપની સ્પીડફૅમ કંપનીએ, ફ્લૅટ સરફેસ સુપર ફિનિશિંગ માટે આયાત થનારા મશીનો, કન્ઝયુમેબલ તથા માપન ઉપકરણોની સામે સક્ષમ સ્વદેશી વિકલ્પ ગ્રાહકોને ઉપલબ્ધ કરાવેલ છે.